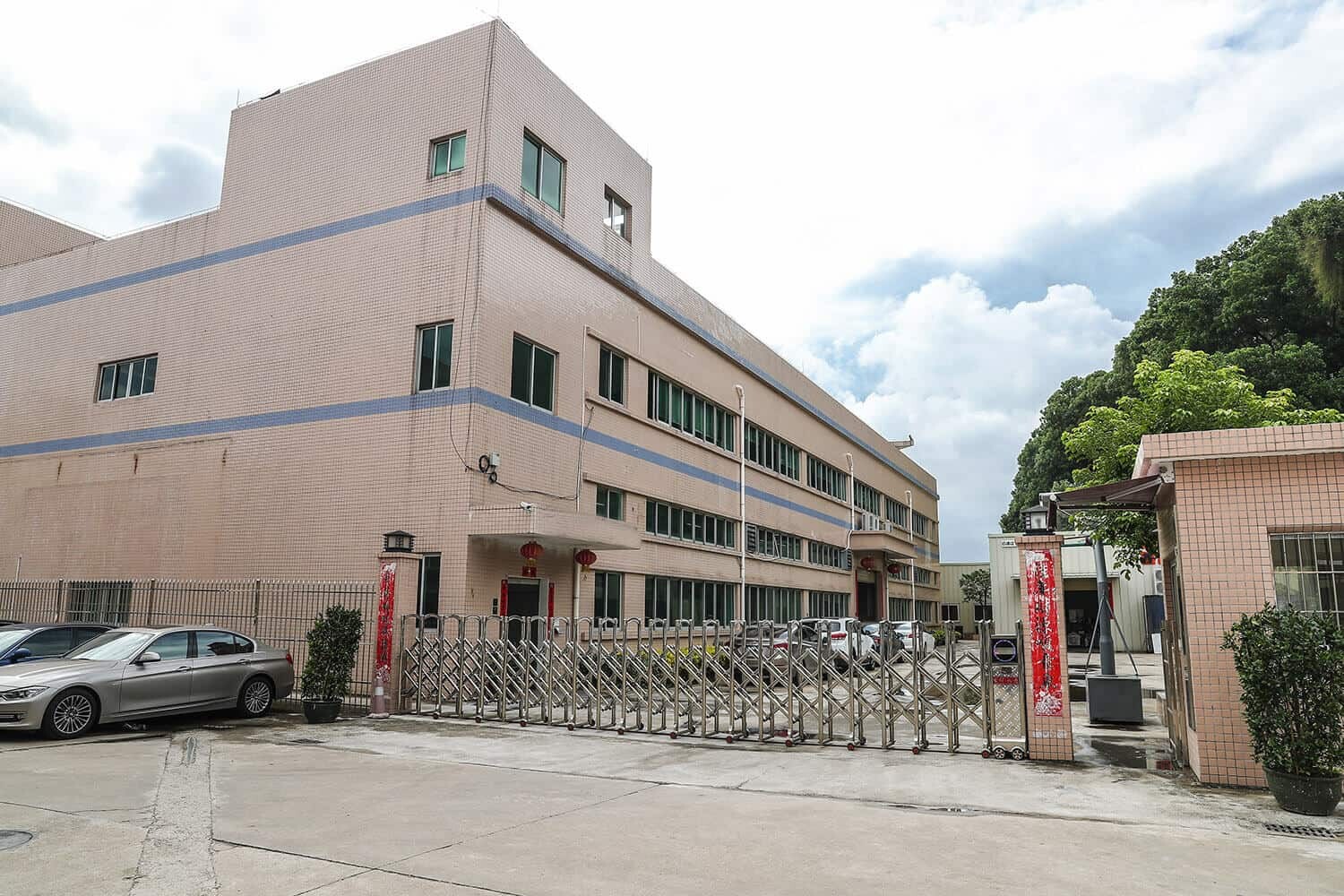
Rapid Prototyping & Rapid Manufacturing Expert
Specialize in CNC machining, 3D printing, urethane casting, rapid tooling, injection molding, metal casting, sheet metal and extrusion
What conditions should a competitive CNC machining shop have?
A competitive CNC machining shop is usually a small but professional manufacturing facility dedicated to delivering custom parts and prototypes in a short time. CNC machining is one of the most popular ways to manufacture prototypes and low-volume parts, and today let we discuss for meet customers’ needs, what conditions required for a competitive CNC machining shop.
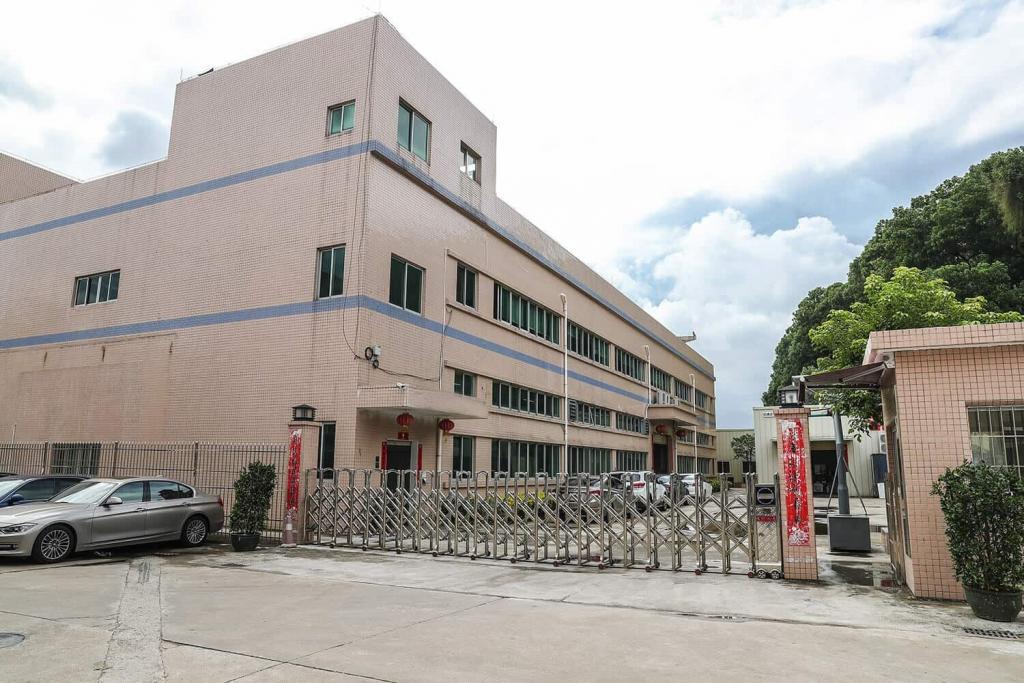

OverView Competitive CNC Machining Shops
Advanced technology and experience reserves, with the ability to deal with tight tolerances and complex geometry parts.
Ability of design validationand provide constructive advice to clients.
Ability to process different metals, plastics and other special materials, such as titanium alloysand other hard materials.
Ability to specialize in specific industries such as aerospace, automotive, medical, etc.
Ability to provide holistic services covering the entire product life cycle.
Turn your ideas into tangible products in a short time.
Enough productioncapacity for machining the parts in high volume.
Resource integration capabilities, such as a strong supply network, logistics and transportation, etc.
Necessary hardware conditions
The hardware of each competitive CNC machining shop varies by plant size and area of expertise, but any real CNC machining shop should at least have the necessary equipment and machinery.
CNC Milling machines. This is the basic equipment of any real CNC machining shop. CNC Milling machine is a kind of machine that uses a cutting tool to cut the metal or plastic by a rotating motion and can perform different operations, from creating planes to machining threads.

Multi-axis CNC milling machines. Also know as a CNC machining center, is usually one of the necessary equipment in any CNC machining shop. CNC Machining Center is a very advanced machine with more complex extensions function that can perform cutting operations on 3, 4 or 5 axes, and even more advanced ones can operate on 7 axes. It should be emphasized that more axes means more complex parts can be machining. However, making simple parts with a multi-axis CNC machine is really not the best idea because multi-axis machines require longer configurations. The process involves creating a 3D model in a CAD/CAM software program and CNC programming, covert 3D files into G code for the CNC machining center to execute commands.

CNC Lathing machines. Initially, lathing machine was a manually operated machine, but now it is generally referred to as a CNC turning machine. In contrast to CNC milling machines, CNC turning machine do not use rotating cutting tools, but rotate the part approaching the tool in a liner motion. Usually used for machining round parts, knurling and surface finishing.

Grinding machines. Grinding machines are used to grind the surface of a part to remove small pieces of material for a higher surface finish. The material and type of grinding wheel used in grinding machine depends on the desired surface finish. Of course, the higher requirements of surface finish will mean the cost higher also.

Band sawing machine. Band sawing machine is mainly used for sawing carbon structural steel, low alloy steel, high alloy steel, special alloy steel and stainless steel, acid-resistant steel and other metal materials. And band sawing machines can cut the rods or sheets into smaller pieces materials which can be easier for CNC machining.

Dilling machine. Drilling machine refers to a machine tool that mainly uses a drill bit to machine holes in a workpiece. Drilling machine structure is simple, processing accuracy is relatively low, can drill through holes, blind holes, replacement of special tools, can be expanded, countersink, reaming or tapping and other processing.

Electrical Discharge Machining (EDM). Widely used in the manufacture of various metal molds and mechanical equipment, using current sparks to evaporate particles from the surface. When CNC machining is not in place and cannot meet the requirements of the parts, EDM is required for machining.

Tools for surface treatment. A competitive CNC machining shop prepared some painting tools at least, but a competitive CNC machining shop is equipped with polishing, anodizing and sandblasting process.

Coordinate Measuring Machine (CMM). Measurement and inspection tools are necessary to guarantee high-quality results. CNC machining shops need it to verify dimensions and tolerances of the part. Therefore, a CMM is very important because it can measure almost any geometric shape very accurately.

Vernier caliper. As above mentioned, any competitive CNC machining shop will request measurement and control tools. Vernier caliper is another measuring tool that you can find it in any CNC machining shop. This tool allows to measure internal and external dimensions as well as depth.
Micrometer and Pin Gauge. For higher precision measurements, micrometers work better than other measuring tools. It can also measure different dimensions such as length, thickness and depth. Pin gauges are great tools for small holes where you need to check diameters and their tolerances.

QC and QA in Competitive CNC Machining Shops
Inspection and validation are critical to high-quality results for CNC machining shops. hat’s what quality control and quality assurance are all about. Now, how does QC and QA in CNC machining shop? The most common actions CNC machining shops take for QC and QA are as follows:
Inspection for raw material
The quality control inspector inspects visually whether the raw materials can be used for prototype manufacturing. If necessary, it need to be sent to professional inspection institutions for do inspection, after get the SGS report, then be able use for CNC machining.

Mechanic’s inspection
The machine operator is the first person who can determine if the parts are meeting expectations or if there are any quality issues. They can verify the quality of parts during operation or removed from CNC machine.

Process exploration
CNC machining shop often have highly advanced machines that enable them to verify tolerance using automated in-process detection as part of the CNC program.
QC inspection department
This is the third step of quality inspection and assurance, following process exploration and operator verification. The quality control department relies on advanced auxiliary equipment such as CMM, vernier calipers, Pin Gauge and other tools for a third inspection of the part.

Human Factors
A competitive CNC machining shop must be staffed with a certain number of trained and experienced engineers, technicians and operators. And for many, the machine and their technology seem to do all the work, but that’s not the case. Finally, without the correct input, the machine cannot obtain high-quality results. Machines and their technological developments made the work easier, more efficient and more accurate, but some skills are still required to make it work as intended. The most important skills for an excellent machinist include:
Problem-solving skills to correct mistakes, find ways to improve and realize the full potential of machines.
Strong technical knowledge of CAD/CAM software programs, etc.
Attention to detail to identify potential problems and avoid accidents that could result in serious injury.
Mathematical skills to understand complex instructions and ensure correct dimensions and tolerances for the most complex geometries.
Endurance to work in stressful and demanding conditions.
Safety at the Competitive CNC machining shop
Having different types of machines and tools working at the same time can become dangerous if without the right measures and actions are taken to ensure safety. Any CNC machining shop at least to consider the following points for guarantee safety:
Provide the employees with the appropriate apparel, including protective equipment such as goggles and safety shoes.
Make sure operators are in the right physical and mental conditions to operate the machines. A sick or tired operator could put the entire shop in danger, not to mention one under the effects of alcohol or drugs.
Avoid distractions and prevent machines from being unattended.
Keeping machines in the right conditions by performing periodic maintenance and updates.
Having clear hazards control guidelines and an emergency plan.
Having an appropriate waste management plan.
If you are ready to start a new project, it is important to choose a long-term CNC machining shop. Sign a non-disclosure agreement to make sure your ideas and designs are safe. Good and effective communication is always essential so that the CNC machining shop can truly understand your needs and expectations.