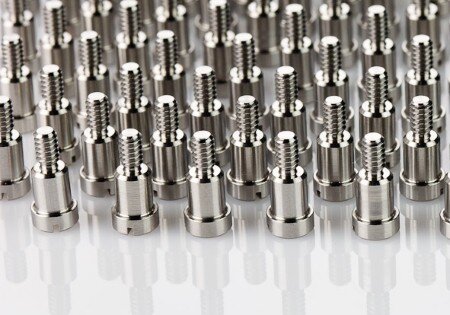
Rapid Prototyping & Rapid Manufacturing Expert
Specialize in CNC machining, 3D printing, urethane casting, rapid tooling, injection molding, metal casting, sheet metal and extrusion
The Finishing Services For CNC machined parts
In the field of CNC precision machining, the working performance and service life of parts with high requirements for strength and toughness are closely related to their surface properties. And the improvement of surface properties cannot be achieved solely by relying on materials, as it is very uneconomical, but it is necessary to make its performance meet the standard in actual processing. At this time, we have to use various finishing services technologies. Surface treatment is the process of artificially forming a surface layer on the surface of a substrate that is different from the mechanical, physical and chemical properties of the substrate through specific processing techniques. In addition, for CNC machining precision metal parts, in order to meet the purpose of wear resistance, corrosion resistance, insulation, decoration, improving service life or adding other special functions, we generally adopt specific finishing services to meet the requirements. For the surface treatment of customized metal parts, the common techniques we see are anodizing, electroplating, electrolytic polishing, passivation, brushing, sandblasting, painting and powder coating, etc.
Electrochemical oxidation of metals or alloys. Aluminum and its alloy parts form an oxide film (insulation) on the aluminum parts (anode) under the action of an applied current under the corresponding electrolyte and specific process conditions. Anodizing usually refers to sulfuric acid anodizing unless otherwise specified. In order to overcome the defects of surface hardness and wear resistance of aluminum alloy parts, expand the scope of application and prolong the service life, surface treatment technology has become an indispensable part of the use of aluminum alloy parts, and anodizing technology is the most widely used and the most economical. At present, there are two main types of anodizing: Type II sulfuric acid anodizing and Type III hard anodizing (hard coating).

Type II Anodizing
The type II sulfuric acid anodizing process is the most common method for anodizing.The sulfuric acid anodize process films range from .0001″-.001″ thick. The overall thickness of the coating formed is 67 percent penetration in the substrate and 33 percent growth over the original dimension of the part. It is particularly suited for applications where hardness and resistance to abrasion is required.However, where parts are subjected to considerable stress, (such as aircraft parts), the possible presence of the corrosive acid residue is undesirable. The porous nature of sulfuric acid films prior to sealing is used to particular advantage in the production of colored surface finishes on aluminum and its alloys.
The porous aluminum oxide absorbs dyes well, and subsequent sealing helps to prevent color loss in service. Although dyed anodized films are reasonably colorfast, they have a tendency to bleach under prolonged direct sunlight.Some of the colors are: Black, Red, Blue, Green, Urban Grey, Coyote Brown, and Gold. Parts can be treated chemically or mechanically prior to anodizing to achieve a matte (non-reflective) finish.

Sulfuric Acid Anodize Benefits:
Less expensive than other types of Anodize with respect to chemicals used, heating, power consumption, and length of time to obtain the required thickness.
More alloys can be finished.
Harder than chromic anodize.
Clearer finish permits dying with a greater variety of colors.
Waste Treatment is easier than chromic anodize, which also helps to reduce cost.
Sulfuric Acid Anodize Applications:
Optical components
Hydraulic valve bodies
Military weapons
Computer and electronic enclosures
Mechanical hardware
Type III Hard Anodizing
Type III hard anodizing (hard coating), while usually done in a sulfuric acid based electrolyte, is much thicker and denser than the more conventional sulfuric anodize. Hardcoat is specified for aluminum components subject to extreme wear applications where superior abrasion resistance is needed, or corrosive environments where a thicker, harder, more durable coating is necessary.It can also be valuable where enhanced electrical insulation is required. Since hardcoat anodize can be built up to several thousandths in some cases, it makes this type of anodize a candidate for salvaging worn or mis-machined components.

Hard Anodize Features:
Improved wear resistance
Non-conductive
Can repair worn surfaces on aluminum
Improve parts surface for slide applications
Can be black dyed; other colors less decorative
Finish is harder than tool steel
Can be ground or lapped
Hard Anodize Applications:
Valves
Pistons
Sliding Parts
Hinge Mechanisms
Cams
Gears
Swivel Joints
Insulation Plates
Blast Shields
Finishing Services:Electroplating
Electroplating is the process of applying one or more layers of a metal to a part by passing a positively charged electrical current through a solution containing dissolved metal ions (anode) and a negatively charged electrical current through your part to be plated (cathode). The history dates back to the ancient Egyptians who would coat metals and non-metals with gold or a process known as “gilding”, the first known surface finish. Some metals apply more evenly than others, but the use of electricity means that the metal being deposited flows more easily to high current areas or the edges of a part. This tendency is especially pronounced on complex shapes or when trying to plate the inside or ID portion of a part.

Types of Electroplating:
Cadmium
Copper
Gold
Hard Chrome
Nickel
Silver
Tin
Tin-Lead
Zinc
Zinc-Iron
Black Nickel
Black Chrome
Features of Electroplating:
Corrosion resistance
Wear Resistance
Appearance
Lubricity
Solderability
Applications for Electroplating:
Military weaponry
Medical diagnostic instruments
Optics
Tools and dies
Aircraft components
Machine components
Electronics & computer devices
Enclosures, chassis and heat sinks
Mechanical assemblies
Finishing Services:Electropolishing
Electropolishing is the process of smoothing and/or brightening a metal surface anodically in a concentrated acid or alkaline solution. Set up to perform it on either Stainless Steel or other Nickel rich alloys. While it can be done on many base metals as a preplate operation, it is commonly done on Stainless Steel as a final finish. It provides a chemically and physically clean surface and removes any mechanical surface asperities which may be detrimental to the production of uniform and pit-free electroplated surfaces or the future performance and appearance of a Stainless Steel product. It helps to deburr machined edges and holes as well as removes any imbedded iron from the manufacturing process. The current is greatest on the outside edges and outside corners of parts, which are left especially smooth. The longer the process is applied, the greater the amount of metal that is removed: holes can be enlarged, threads can be rounded, and sharp edges can be smoothed.

Features of electropolishing:
Improved Appearance
Burr Removal
Cost effective microfinishing
Avoidance of friction, leakage, and wear
Passivation/Cleaning
Applications of electropolishing:
Medical Implants & Devices
Food processing & handling equipment
Pharmaceutical/laboratory equipment
Gears & Splines
Finishing Services:Passivation
Passivation is used to improve the surface condition of stainless steel by dissolving the iron that is embedded in the surface by forming, machining, or other manufacturing steps. If allowed to remain the iron corrodes and often gives the appearance of large or small rust spots on the stainless steel. In order to prevent this condition on the finished parts, they are given a passivation treatment. This treatment, which consists of immersing the stainless steel parts in a solution of nitric acid without oxidizing salts for a specific period of time, will dissolve the embedded iron and restore the original corrosion-resistance surface by forming a thin transparent oxide film. Passivating is used as the cleaning operation for castings, stampings and finished machine parts by immersing the parts.

Features/Benefits:
Stainless steel does not have to be plated to achieve maximum corrosion protection Passivate
Provides a superior clean surface
No rust discoloration of the stainless steel when in service
Surface preparation for other finishes such as priming or painting
Passivated stainless steel will not react with other materials because of iron contamination
Applications:
In general where iron contamination is detrimental to a part’s performance
Sterilization of tools and equipment in the medical field including implants
Food industry such as mixers, tanks, handling equipment, shielding, and fasteners
In the architectural or marine fields where surface finishes must last for decades
Aerospace fuel system controls
List of Processes/ Specifications:
AMS 2700
AMS QQ P 35
ASTM A 380
ASTM A 967
MIL S 5002
Finishing Services:Brushing
Surface brushed treatment is a surface treatment method that forms lines on the surface of the workpiece by grinding the product, which has a decorative effect. Because the surface brushed treatment can reflect the texture of metal materials, it has been loved by more and more users and more and more widely used. The processing method of surface brushed should choose different processing methods according to the requirements of brushing effect, the size and shape of different workpiece surfaces. There are two ways of surface brushing treatment: manual brushing and mechanical brushing.

Finishing Services:Sandblasting
The process of cleaning and roughening the surface of the substrate by the impact of high-speed sand flow. The compressed air is used as the power to form a high-speed jet beam to spray the spray material (copper ore sand, quartz sand, emery, iron sand, Hainan sand, etc) to the surface of the workpiece to be treated at high speed, so that the appearance or shape of the outer surface of the workpiece surface changes. Due to the impact and cutting effect of the abrasive on the surface of the workpiece, the surface of the workpiece can obtain a certain degree of cleanliness and different roughness, so that the mechanical properties of the workpiece surface are improved, thus improving the fatigue resistance of the workpiece, increasing coating adhesion, prolongs the durability of the coating film and facilitates the leveling and decoration of the paint also.

Finishing Services:Powder Coating
Powder costing uses the phenomenon of corona discharge to make the powder coating adsorb on the workpiece. The process of powder coating is: the powder spray gun is connected to the negative electrode, the workpiece is grounded (positive electrode), the powder coating is fed into the spray gun by the powder supply system by means of compressed air gas, and a high voltage generated by a high-voltage electrostatic generator is added to the front of the spray gun. A dense charge is generated near it. When the powder is sprayed from the gun nozzle, it forms a circuit to form charged paint particles, which are attracted to the workpiece with the opposite polarity due to the electrostatic force. The more the accumulation is, when it reaches a certain thickness, due to the electrostatic repulsion, the adsorption will not continue, so that the entire workpiece can obtain a powder coating of a certain thickness, and then the powder will be melted, leveled, and solidified by heat, that is, forms a hard coating on the surface of the workpieces.
