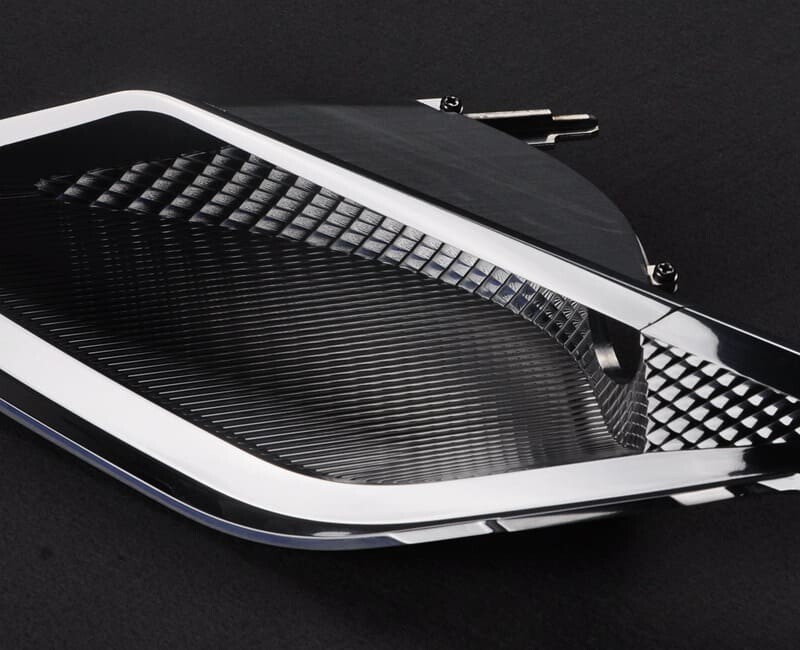
Rapid Prototyping & Rapid Manufacturing Expert
Specialize in CNC machining, 3D printing, urethane casting, rapid tooling, injection molding, metal casting, sheet metal and extrusion
Talk about the experience of manufacturing aluminum reflector
People enjoy the convenience of cars thanks to the constant pursuit of perfection by car designers.In the automotive development process, a verification program is essential, which requires customizing a small number of parts to check whether the material, size, assembly, etc. are suitable. Manufacturing a few or dozens of parts is a huge challenge on an automotive production line, which is why designers often turn to prototyping companies for help. Traditional, long-life tooling is expensive and usually not suitable for small batch needs.
Professional rapid prototyping companies are often the fastest to understand the designer’s intentions and provide customized aluminum machining services to meet the needs of small batches or even individual parts.


Of all the lighting systems, automotive lighting is one of the most challenging projects, and only the most experienced prototype builders can achieve the perfect result that the designers are after. Aluminum reflectors not only affect the appearance of the headlights, but most importantly play an optical role. We saw at the auto show that the headlights of BMW and Audi, shining charming lights, left a deep impression on us. In the process of prototyping an aluminum reflector for a high-end car, designers especially want the prototype builder to understand all the tiny details they really care about.
1. What is the best process for machining prototypes of aluminum reflectors?
For automotive parts, additive manufacturers often offer several machining options for different needs. Such as CNC machining, 3D printing (additive manufacturing), etc.
3D Printing. 3D printing is gaining popularity in the automotive world, making everything from interior components to entire chassis and even tires. 3D printing has many advantages, including making lighter parts, less waste, shorter manufacturing time, and lower costs. However, there are some car parts that are not ideal for 3D printing – such as headlights. Since SLA is a layer-by-layer process, the final product tends to show layer lines, while SLS cannot achieve the mirror-like surface finish of optical components.

CNC Machining. CNC machining can cut almost any metal and plastic, and has many advantages such as stable precision and the ability to manufacture complex parts. It is the best choice for manufacturing aluminum reflectors. The aluminum reflector must have a good surface roughness, generally lower than Ra0.2μm, to achieve a mirror gloss effect. As an optical component, the accuracy of the aluminum reflector should be controlled within 0.05mm, which also determines that CNC milling is the best choice.
As one of the automotive lighting components, the aluminum reflector needs to cooperate with other parts and assemble them together to form a whole. This means that the structure of the index reflector is very complex, generally requiring 5-axis CNC machining. In most cases, due to the assembly structure on the back of the aluminum reflector, auxiliary working tools such as WEDM/EDM are needed to clean the corners.

2. Selection of materials
In the prototyping of automotive lighting components, the most commonly used aluminum alloys are 2024, 5052, 6061 and 7075. For parts like bicycles, we can simply choose Al-6061-T6 because it is easy to process and the machining cost is also low. However, Al 7075-T6 is usually used for aluminum reflectors that are installed on luxury cars and require specular gloss. This material has high hardness, light weight, and a very glossy surface after processing. It is also widely used in the fields of automobiles and aerospace, including wheel hubs and wing lights.
3. Processing technology
5-Axis CNC machining. For complex surface features, in order to ensure the best surface quality under appropriate milling conditions, minimal disassembly processing, and to evaluate the best fit of optical surface and PCB holder. The 5-axis CNC linkage machining uses a ball end milling cutter or a diamond milling cutter below D0.5mm, and the machining radius of the inner corner is R0.1-R0.15mm. The results can perfectly present the optical details required by designers, and help optical engineers to participate in the performance evaluation of automotive lamp samples, analyze problems, and propose solutions.

EDM. Because the structure of the car light is quite complicated and there are many details, even a high-precision 5-axis CNC cannot complete the machining parts at one time. This requires CNC programming engineers to have rich experience in the manufacture of prototype lamps, and it is necessary to discuss the processing feasibility of design drawings. For the aluminum reflector, the critical optical surface will be milled by 5-axis CNC, but on the back side, there are some important assembly structures that are difficult to machine by CNC milling, because it will leave fillet radii at the corners, which is not conducive to assembly. Therefore, technicians need to make copper electrodes and use EDM as an auxiliary process to help clean up the corners.
Usually, the EDM machining process will take a lot of time.

Finishing Services. In the late stage of prototyping, there is still a lot of work to be done. Among them, manual post-processing such as deburring, polishing, and electroplating is particularly important, which will directly determine the final appearance and performance.

In order to further achieve a specular finish, there are two ways to achieve this. One is manual polishing, the surface can be mirror luster after polishing. However, the requirements for the operator are very high, and they must be very careful during the handling process, because some optical parts need to maintain sharp edges, and the polishing process may leave stains on the edges. Another method is electroplating, a good milling finish meets the requirement of no impurities before electroplating, and the final surface can be very bright and beautiful.