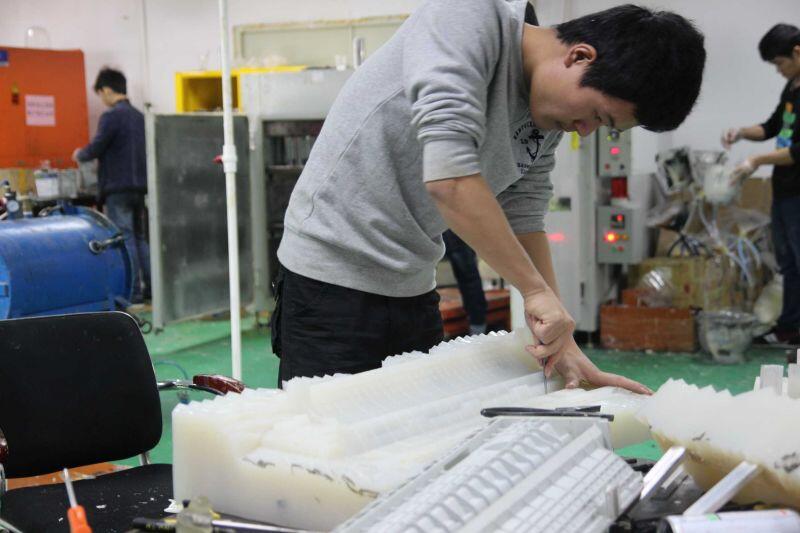
Rapid Prototyping & Rapid Manufacturing Expert
Specialize in CNC machining, 3D printing, urethane casting, rapid tooling, injection molding, metal casting, sheet metal and extrusion
Material Selection for Vacuum Casting Process
Vacuum casting, also known as Urethane casting or Polyurethane casting, is a very diverse manufacturing process that utilizes silicone molds to create high-quality plastic and rubber parts under vacuum.
In some cases, it is comparable to injection molding, which makes vacuum casting parts especially suitable for fit and function testing, and is one of the common ways to manufacture small batches of plastic parts.

1. Advantages of vacuum casting
• Achieve high precision and meticulous detail.Vacuum casting ensures great attention to detail in the final product. The original part has the most complex geometry and the replica looks very similar to the original.
• High quality.Parts produced by vacuum casting are of high quality. The wide range of materials selection allows for a wider choice of flexibility, hardness and stiffness in the product.
• Reduce manufacturing cost.Compared with 3D printing, CNC machining, vacuum casting process is very cost-effective. Silicone molds are much less expensive than aluminum or steel molds.
• Fast turnaround.Vacuum casting takes less time to manufacture parts, which may take 7 to 10 days to make about 200 functioning prototype parts. This method is also great when you are making 2000+ products.


2. Technical Specifications of Vacuum Casting
Turnaround Time | Up to 50-200 parts within 24 hours to 5 business days |
Material Selection | Different Variety of materials are available for selection |
Accuracy | (lower limit of ±0.3 mm for dimensions less than 100 mm) |
Minimum Wall Thickness | To ensure close tolerance requirements, a minimum wall thickness of 0.75mm is required. Recommended wall thickness of 1.5mm. |
Maximum Part Size | Limited by vacuum chamber dimensions (1900 x 900 x 750 mm) and product volume (maximum volume: 10 liters) |
Typical quantities | Up to 25 parts per mold, depending on part complexity |
Surface Finish | From glossy to matte finish |

3. Material Selection for Vacuum Casting
Materials used in vacuum casting include thermoplastics, rubber and resins, all of which can mimic specific properties and characteristics:
Appearance quality
Surface Texture/finish
Transparency/Translucency
Rigidity
Flexibility
Strength
Hardness
Temperature resistance
Ultraviolet Rays
Color
Vacuum cast parts are used in a wide range of applications including automotive and aerospace, pharmaceutical and medical, telecommunications and engineering, food production and consumer goods work. Materials must accurately model the same wide range of industrial materials, including ABS, polycarbonate, polypropylene, glass-filled nylon, and elastomeric rubber.


Vacuum cast materials can simulate the following production materials and properties:
*Rubber—high elasticity
*ABS – high rigidity and strength
*Polypropylene and HDPR – high elasticity
*Polyamide and glass-filled nylon – high rigidity
*Polycarbonate and PMMA – Shock resistant, translucent, high temperature resistant
*Filled ABS – fire resistance and flame retardancy
Based on the inventory of DDPROTOTYPE, a well-known rapid prototyping manufacturer in China, offering 26 carefully selected polyurethanes similar to rubber, PP, ABS and PC. These materials offer an excellent variety of properties.
Material | Comment | Axson Code |
STAR-PU Transparent Rubber | Transparent rubber substitute. Variable hardness, 40 – 70 Shore A. Translucent colors possible. | (Hei-Cast) |
STAR-PU ABS | Flame retardant resin (UL94-V0 specification) | (Hei-Cast) 8263 |
STAR-PU Silicone | Translucent silicone that can be used as VC mold tool and also to fabricate VC part. | ESSIL 296 |
STAR-PU Silicone | Translucent and Food Grade. It is a platinum cured silicone. | HY-E635 |
STAR-PU High-Temp ABS 120C | High temp, most popular ABS compound in the EU. Auto/medical/chemically stable – up to 40 parts per silicone tool. | PX 223-HT |
STAR-PU PC | Transparent. Mainly simulates filled ABS or PC. | PX 527 |
STAR-PU Classic ABS | This is the classic and most popular ABS compound. | UP 4280 |
STAR-PU Classic PP | PP resin compound – living hinges possible (typically 30 to 50 bends before breaking). | UP 5690 |
STAR-PU PMMA (Acrylic) | UV stable. Great for glossy, clear parts. Can be tinted or colored. This is the classic acrylic substitute. | UPX 5210 |
STAR-PU Rubber | Rubber/TPE resin. Variable hardness, 40 – 85 Shore A. Can be over-molded. | UPX 8400 |