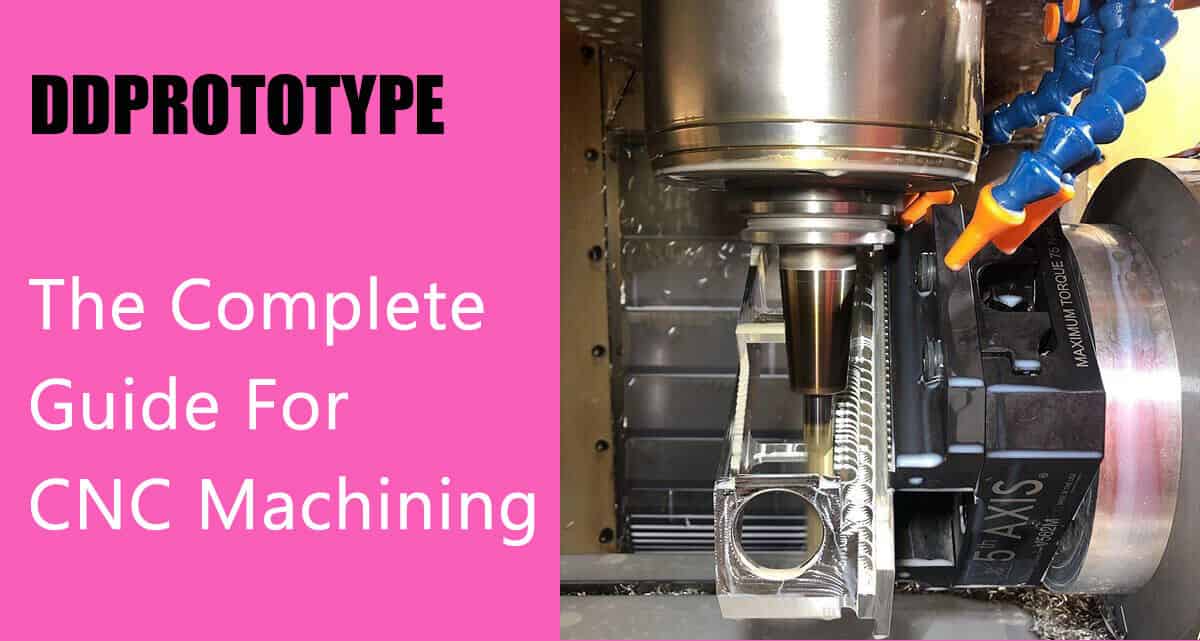
Rapid Prototyping & Rapid Manufacturing Expert
Specialize in CNC machining, 3D printing, urethane casting, rapid tooling, injection molding, metal casting, sheet metal and extrusion
The Complete Guide For CNC Machining
This paper introduces the complete guide of CNC machining in detail, including advantages and disadvantages, design rules and techniques, material selection, cost reduction, finishing service, etc., to help designers around the world to transform their ideas into ideal plastic or metal parts. AS a online cnc machining service shop,We believe ordering custom parts ought to be simple, fast, and straightforward. the concept of DDPROTOTYPE is to provide due contribution to the world’s manufacturing industry, committed to the prototype machining and Low-volume manufacturing of metals and plastics. We have 20 years of CNC machining experience, 3000 square meters of workshop, dozens of 3-axis and 5-axis CNC machines and ancillary equipment from Germany, the United States and Japan, such as EDM / WEDM machine from Japan and Hexagon CMM. Make sure that the designer’s whole energy is focused on product design. DDPROTOTYPE has already served 350 + customers in more than 50 countries around the world, including many of the world’s top 500 enterprises, such as Areva, Olympus, ABB, etc.Let DDPROTOTYPE become a part of your supply chain as Your Online CNC Machine Shop.
If you have any questions, please contact info@ddprototype.com.
What is CNC machining process?
CNC machining processes raw materials into final form by subtracting and removing materials. Drilling holes, channels or voids to make metal or plastic blanks into parts with different taper, diameter and shape. This is in sharp contrast to other types of processing (e.g. additive manufacturing), where materials are added and layered to produce parts of specified shape. This is also in contrast to injection molding, in which a mold is used to inject material in different material states and form shaped parts. CNC machining is widely used for various materials, including metals, plastics, wood, glass, foam and other composite materials. This versatility makes CNC machining a popular choice in the whole industry and enables designers and engineers to manufacture parts efficiently and precisely.

CNC machining operation follows four stages
Part design
Parts produced by CNC machining usually start with CAD software as the initial design. During the design phase, the engineer will carefully consider all aspects of the final product required, such as the parameters for optimizing performance, the working conditions of the final part, and the acceptable level of tolerance variation.
Design conversion
After the initial design phase, CAD models must be converted into functional CNC programs using computer aided manufacturing (CAM) software. CAM software can extract geometric requirements from original CAD model files and convert them into CNC compatible programming languages (such as G code or M code), which will determine the mechanical operation of the machine.
CNC machine tool preparation
Next, the CNC machine operator must set up the machine and materials according to the specifications required by the CNC program. The operator will ensure that the correct cutting or drilling tool is correctly installed and matched with the appropriate drill or end mill. The operator must also set up the workpiece, usually in a fixed fixture or directly mounted on a CNC machine tool.
Performing programmed operations
Finally, CNC machine operators perform the required mechanical processes. During operation, CNC program precisely controls the movement of the machine tool.
CNC machining advantages: timely, reliable, accurate and powerful
CNC milling and turning are highly accurate and repeatable processes. A tolerance of + / – 0.001 “– 0.005” can be achieved according to specifications. The machine can be programmed to run reliably 24 hours a week, 7 days a week if necessary, so CNC milling is one of the best ways to produce parts on demand. Using standard tools, CNC machining is particularly valuable for creating custom disposable parts, such as replacing old parts or providing customers with specialized upgrades. It can also be considered to expand the single piece production scale to more than 10000 units. Depending on the number, size and complexity of the equipment, the turnaround time for components can be as short as one day. Through transportation and delivery, the deadline can be met in a week.
Another major advantage of CNC machining technology is the achievable mechanical properties. All desirable mechanical properties of the selected metal or plastic can be retained by cutting the blank material instead of hot deforming it as in injection molding or additive manufacturing. CNC milling and turning can process more than 50 industrial grade metals, alloys and plastics. This selection includes aluminum, brass, bronze, titanium, stainless steel, peek, ABS and zinc. The only material requirement for CNC machining is that the parts have enough hardness for fixing and cutting. In order to obtain the most cost-effective CNC machining parts, it is suggested to expand the production capacity to disperse the cost of each part. When the number of CNC machining reaches dozens or hundreds, the unit price will gradually decrease. Structured mass production and transportation of CNC parts can help reduce waste or inventory costs.

Disadvantages: the cost of geometric complexity
One trade-off when using the high performance of CNC machining is that geometric complexity comes at a cost. Simple, bulky parts are the best design for CNC milling and turning. Although the degree of use of this tool is related to the number of shafts on the machine tool, there are always some design limitations due to the influence of the tool. In other words, the more axes you use, the more complex the function. Another trade-off is that the start-up cost of CNC processing may be high. There must be trained professionals to set up, load and program tools on CNC milling machines and lathes. Fortunately, this cost is fixed, so it will become more economical by using the same settings for multiple parts. Money can also be saved by repositioning parts to a minimum. Machining on shafts of 5 or more axes is sometimes more economical in polyhedral geometry because it does not require manual repositioning of parts.
CNC milling
In CNC milling, the parts are installed on the machine and the material is removed by using a rotary cutting tool. The following is an overview of the basic CNC milling process:First, the CAD model is transformed into a series of commands (g codes) that can be interpreted by CNC machine. This is usually done by the operator on the machine using the technical drawings provided.A piece of material (called a blank or workpiece) is then cut into a certain size and then placed on a built platform using a vise or directly mounted to the machine. Accurate positioning and alignment is the key to manufacturing accurate parts, for which special measuring tools are usually used.

Next, a special cutting tool is used to rotate at a very high speed (kilo RPM) to remove the material from the blank. It usually takes several passes to create a designed part. Firstly, the material is removed quickly with low precision to provide approximate geometry for the blank. One or more finishing passes are then used to produce the final part.If the model has features that cannot be achieved by the cutting tool in a single setting (for example, if the back side has slots), you need to flip the part and repeat the above steps.
After machining, parts need deburring. Deburring is a manual process to remove small defects left on sharp edges due to material deformation during machining (e.g., defects due to the drill bit being located far from the through hole). Next, if tolerances are specified in the technical drawings, the key dimensions are checked. The part can then be used or post processed.Most CNC milling systems have three linear degrees of freedom: X, y and Z axes. More advanced systems with five degrees of freedom also allow the bed and / or bit (A and B axes) to rotate. The 5-axis CNC system can produce parts with high geometric complexity and eliminate the need for a variety of machine tool settings.

CNC turning
In CNC turning, the parts are installed on the rotating chuck and the fixed cutting tools are used to remove the material. In this way, parts symmetrical along its central axis can be made. Turning parts are usually produced faster (and cheaper) than milling parts.
This is a summary of the steps to be followed in CNC turning :
Firstly, G code is generated from CAD model, and then cylinder with appropriate diameter is loaded into CNC machine tool.
The part begins to rotate at high speed, and the stationary cutting tool tracks its profile and gradually removes material until the geometry of the design is created. Holes along the central axis can also be made using a center drill and an internal cutting tool.
If the part needs to be flipped or moved, repeat the process. Otherwise, the parts can be cut from the stock and can be used or further post processed.

A typical CNC turning part is made by removing material from a cylindrical blank.
Generally, CNC turning systems (also known as lathes) are used to manufacture parts with cylindrical profiles. Non cylindrical parts can be manufactured using a modern multi axis CNC turning center equipped with CNC milling tools. These systems combine the high productivity of CNC turning with CNC milling functions, and can produce various geometries with rotational symmetry, such as camshaft and radial compressor impeller. In CNC turning operation, when the workpiece rotates at high speed on the spindle, the cutting tool remains stationary. CNC turning can rapidly produce cylindrical parts with strict tolerance. For example, ddprototype CNC lathes can produce parts up to 152 inches in diameter and 240 inches in length, while still maintaining a strict tolerance of ± 0.001 inches.
Because the boundary between milling and turning systems is fuzzy, the rest of this paper focuses on CNC milling, because it is a more common manufacturing process.

Types of CNC machine tools
The most common types of CNC machines are those that use cutting tools to remove excess material from the workpiece. Although CNC machines operate with water jet cutting and electrical discharge machining (EDM), this guide will focus on 3-axis and multi axis CNC machines.
3-axis CNC machine tool
3-axis CNC milling machines are very common because they can be used to produce the most common geometry. They are relatively easy to program and operate, so the start-up processing cost is relatively low. Tool access may be a design constraint in CNC milling. Since only three axes are available, some areas may not be accessible. If the workpiece only needs to be rotated once, this is not a big problem, but if it needs to be rotated many times, the labor and processing costs will increase rapidly. The 3-axis machine allows the cutting tool to move along straight three-dimensional vectors (up and down, left and right, forward and backward).

Multi axis CNC machine tool
Multi axis CNC machine tool is similar to 3-axis machine tool, but the degree of freedom of mechanical motion is higher. For example, multi axis machine tools can use rotary and diagonal cutting operations. There are three main types of multi axis CNC machine tools:
Indexing 5 axis CNC milling machine
Even if the milling machine can only cut along three linear axes during operation, the operator can still rotate the bed and cutter head for the next cutting between the two operations, thus improving the forming ability.
Continuous 5 axis CNC milling machine
This machine type allows continuous motion along three linear axes and two rotating axes during operation. This enables the operator to create highly complex tables from the target artifact.

The milling turning center
The milling turning center combines the functions of CNC lathe and CNC milling machine. The workpiece can be rotated at high speed or precisely positioned on the spindle for milling operation.
Of all the various machine configurations, the simplest setup is 3-axis CNC milling, which is usually the cheapest way to make simple parts with high tolerances. When cylindrical workpieces such as screws and couplings are required, CNC turning on a lathe is also a very cost competitive process. Generally, for similar parts, the cost of a lathe is 15% lower than that of a three axis machine tool.
When using 5-axis CNC machining, there are two options: indexing 5-axis CNC milling and continuous 5-axis CNC milling. In 5-axis CNC milling, the workpiece will rotate automatically, making it easier for the cutter to use the milling function. The two extra directions of motion are accomplished between the milling steps without removing the part from its fixture. The difference of continuous 5-axis CNC milling is that the machine can move in all directions at the same time when cutting the workpiece. Both processes eliminate the increased costs and potential human errors associated with manually repositioning the workpiece. Because of these advantages, five axis machining is the best solution for complex parts. Compared with the “basic” 3-axis CNC milling machine, the cost of 5-axis machining is increased, and the indexing 5-axis CNC milling machine is the cheaper of the two. The cost of continuous 5-axis CNC milling is usually more than 20% higher than that of indexing 5-axis machine tool, which is about twice the cost of standard 3-axis milling.

Design CNC machining parts – CAD model design
The concept of CAD is machining point. In addition to the design requirements directly related to the final application of the product, the engineer must also pay attention to the functions and limitations of the CNC machine tools to be used for actual cutting operations. Engineers must convert the original CAD model file to a CNC compatible format, such as open source step or IGES format, or to a more restricted format, such as IPT or sat. It is also a best practice for engineers to create technical drawings that will be sent with digital CAD instructions. These drawings are used to verify design tolerances and geometry. Help the machinist identify the salient features of the part; and act as the actual source of validation when problems arise.
Seven rules of CNC machining process
Rule 1: all roads lead to radius
Since most drills are cylindrical in design, this means that any internal cuts you make will also produce curved corners / edges, also known as rounded corners. When designing parts with internal fillet, follow the principle of “bigger is better”. The resulting angle will be half the diameter of the tool used.
Use a non-standard radius, such as 1.25 mm instead of 1 mm, to allow a certain tool clearance to cut corners. Where possible, different wall and floor radii should also be used for design so that the same tool can be used throughout the process.
The precise measurement of the inner corner will be related to the depth of the cavity being machined. When inserting inner corners and edges, the radius should be greater than one third of the cavity depth.
Rule 2: right angle undercut
To create right angles in CNC machined parts, it is better to add undercuts to the design rather than try to reduce the radius of corners to achieve similar results. To avoid the additional cost of custom tools, design undercut slots of standard size, i.e. 3 mm to 40 mm wide in millimeters. Due to the shape of the tool used, undercut should be as shallow as possible. The maximum depth that the undercut tool can reach will be twice the width of the tool head.
Rule 3: fillets can cause cavities
The cavity / cavity depth is usually related to the diameter of the tool used to make the inner fillet. As a guide, the groove depth should be up to 3-4 times the tool diameter. If the depth exceeds 6 times the tool diameter, a larger tool is required. This will sacrifice your corner radius. The cavity width should also be considered when machining the cavity. It is best to keep the depth at 4 times the width, which is a good guide.
Rule 4: tall features, bad vibrations
As with the depth of cavity and pit, the maximum height of tall feature is 4 times of feature width at most. The higher the feature is, the easier it is to vibrate, thus reducing the machining accuracy of parts.
Rule 5: avoid thin walls
Generally speaking, it is better to use thicker walls in part design. As with high walls, vibration increases when thin-walled features are made. Heat must also be considered when processing plastics. Due to the friction of the cutter head, the thinner wall will be easier to soften and warp. As a guide, the minimum thickness of the plastic wall should be between 1.0 and 1.5 mm. The minimum wall thickness in metal parts may be between 0.5 mm and 0.8 mm. If walls are supported, they should be thicker or higher to avoid vibration and tremor.
Rule 6: follow the standard when drilling
There are two kinds of holes to choose in CNC milling: blind hole and through-hole. Regardless of the type selected, the recommended depth and diameter are the same. The hole diameter should be related to the standard bit size of 25.5 mm (diameter over 1 mm) and above. The nominal depth of the hole depends on the maximum diameter of the hole. Typically, the depth of the hole is created equal to 10 times the nominal diameter of the hole.
Rule 7: compliance with thread standards
It is also important to maintain the standard size when creating threads. The larger the thread, the easier the processing. The maximum length should be maintained to 3 times the nominal diameter of the hole. Additional costs are avoided by retaining the ready-made thread size in the part.
CNC material selection guidelines
Proper material selection is essential for CNC machining operations. The choice depends largely on the intended use of the end product. As a subtractive manufacturing process, CNC machining uses raw materials such as metals or plastics to make parts. This block is called a material blank. No matter which material is used, it is very important to select the correct blank size before the production process. In general, it is advisable to select a blank with each size at least 0.125 inch (~ 0.3 cm) larger than the final part size to resolve any inconsistency in the raw material. At the same time, it is important not to use too large blanks to minimize material waste. Another important thing to remember before ordering CNC machined parts is that the choice of materials affects production time and cost. This is because some materials are Machinable better than others, which means they are easier to process. Faster processing speeds eventually translate into lower production costs.

Metals are mainly used in applications requiring high strength, hardness and heat resistance. Plastics are lightweight materials with a wide range of physical properties, which are usually used because of their chemical resistance and electrical insulation properties. Material properties of interest are mechanical strength (expressed as tensile yield strength), machinability (machinability affects CNC pricing), material cost, hardness (mainly for metals) and temperature resistance (mainly for plastics).
You need to examine a range of material properties to determine which material is most suitable for your design, such as:
tensile strength
hardness
It is easy to operate
Chemical resistance
Corrosion resistance
Thermal performance
metal parts
Generally, high ductility metals are easier to process because CNC milling cutters can cut metal more easily and achieve higher efficiency. For example, brass is one of the easiest metals to process because of its good ductility. Aluminum alloy is also very suitable for CNC machining, so it can shorten the production time. Steel, on the other hand, is a solid metal with much lower machinability than aluminum, which means lower productivity and higher costs. However, it is important to remember that different grades of steel have different levels of workability, depending on their carbon content. Steels with very low and very high carbon content are usually difficult to machine. For example, stainless steel 304 with a low carbon content is difficult to machine because it becomes sticky and hardens too quickly. Additives such as sulfur and phosphorus make stainless steel easier to process, such as stainless steel 303. From a machining point of view, carbon steel usually takes four times as long as aluminum, while stainless steel takes twice as long.

Plastic parts
Although thermoplastic plastics can be machined, the material properties of polymers may pose challenges to CNC machining. Firstly, due to the poor thermal conductivity, many thermoplastic plastics will melt or warp when contacting with CNC milling cutter or drill bit. For parts that do not require metal strength and stiffness, thermoplastic offers a cheaper option. In the range of thermoplastic, Delrin (POM), high density polyethylene (HDPE) and ABS have good machinability. Although peek, ULTEM, nylon and many composites are popular for their strength and durability, they are more difficult to process.

Aluminum alloy
Aluminum alloy has excellent strength / weight ratio, high thermal conductivity and conductivity, and natural corrosion resistance. They are easy to process and low in batch cost, so they are often the most economical option for creating custom metal parts and prototypes.Aluminum alloys usually have lower strength and hardness than steel, but can be anodized to form a hard protective layer on its surface.
Aluminum alloy 6061 has the most excellent cutting strength than other aluminum alloy.
Aluminum 6082 composition and material properties are similar to those of 6061. It meets European standards and is therefore more commonly used in Europe.
Aluminum 7075 is the most commonly used alloy in aerospace applications because it has excellent fatigue properties for steel and can be heat treated to achieve high strength and hardness, so it is essential to reduce weight.
Aluminum 5083 has higher strength and excellent seawater resistance than most other CNC aluminum machining and is therefore commonly used in architectural and marine applications. It’s also a great choice for welding.
Material properties:
Typical density of aluminum alloy: 2.65-2.80 g / cm3
It can be anodized
Nonmagnetic
stainless steel
Stainless steel alloys have high strength, high ductility, excellent wear resistance and corrosion resistance, and are easy to weld, machine and polish. Depending on their composition, they can be (basically) nonmagnetic or magnetic.
Stainless steel 304 is the most common stainless steel alloy with excellent mechanical properties and good machinability. It is resistant to most environmental conditions and corrosive media.
Stainless steel 316 is another common stainless steel alloy with mechanical properties similar to 304. Although it has higher corrosion and chemical resistance, especially for salt solutions (e.g. seawater), it is usually preferred for use in harsh environments.
Stainless steel 2205 duplex stainless steel is the highest strength stainless steel alloy (twice of other common stainless steel alloy), and has excellent corrosion resistance. It is used in harsh environments and has many applications in the oil and gas industry.
Stainless steel 303 has excellent toughness, but has lower corrosion resistance than 304. Due to its excellent machinability, it is often used in mass applications such as nuts and bolts for aerospace applications.
The mechanical properties of 17-4 stainless steel (SAE 630 grade) are comparable to 304. It can be precipitation hardened to a very high degree (compared to tool steel) and has excellent chemical resistance, making it suitable for very high performance applications, such as the manufacture of turbine blades.

Material properties:
Typical density: 7.7-8.0 g / cm3
Non magnetic stainless steel alloy: 304, 316, 303
Electromagnetic stainless steel alloy: 2205 duplex, 17-4
Low carbon steel {mild steel}
Low carbon steel, also known as low carbon steel, has good mechanical properties, good machinability and good weldability. Because of their low cost, they can be used for general purposes, including the manufacture of mechanical parts, fixtures and fixtures. Low carbon steel is susceptible to corrosion and chemical attack.
Low carbon steel 1018 is a general alloy with good machinability and weldability, as well as excellent toughness, strength and hardness. It is the most commonly used low carbon steel alloy.
Low carbon steel 1045 is a medium carbon steel with good weldability, good machinability, high strength and impact resistance.
Low carbon steel A36 is a common structural steel with good weldability. It is suitable for various industrial and architectural applications.

Material properties:
Typical density: 7.8-7.9 g / cm3
magnetic
Alloy steel
Alloy steels contain other alloying elements in addition to carbon, thus improving hardness, toughness, fatigue and wear resistance. Similar to low carbon steel, alloy steel is also susceptible to chemical corrosion and corrosion.
Alloy steel 4140 has good overall mechanical properties, as well as good strength and toughness. This alloy is suitable for many industrial applications, but is not recommended for welding.
Alloy steel 4340 can be heat treated to achieve high strength and hardness while maintaining good toughness, wear resistance and fatigue strength. This alloy is weldable.

Material properties:
Typical density: 7.8-7.9 g / cm3
Magnetic
Tool steel
Tool steel is a kind of metal alloy with high hardness, rigidity, wear resistance and heat resistance. They are used to create manufacturing tools (hence the name), such as molds, dies and molds. In order to obtain good mechanical properties, it must be heat treated.
Tool steel D2 is a kind of wear-resistant alloy, its hardness can be maintained at 425 ° C. It is usually used to make cutting tools and dies.
Tool steel A2 is a kind of air hardening general tool steel, which has good toughness and excellent dimensional stability at high temperature. It is usually used to make injection moulds.
Tool steel O1 is an oil hardening alloy with high hardness of 65 HRC. Commonly used for cutting tools and cutting tools.

Material properties:
Typical density: 7.8 g / cm3
Typical hardness: 45-65 HRC
Brass
Brass is a metal alloy with good machinability and excellent conductivity, which is very suitable for applications requiring low friction. It is also often used in architecture to produce parts with a golden appearance for aesthetic purposes.
Brass c36000 is a kind of material with high tensile strength and natural corrosion resistance. It is one of the easiest materials to process, so it is often used in mass applications.

Material properties:
Typical density: 8.4-8.7 g / cm3
Nonmagnetic
ABS
ABS is one of the most common thermoplastic materials with good mechanical properties, excellent impact strength, high heat resistance and good machinability.
The low density of ABS makes it very suitable for lightweight applications. ABS parts machined by CNC are usually used as prototypes before mass production by injection molding.
Material properties:
Typical density: 1.00-1.05 g / cm3

Nylon
Nylon, also known as polyamide (PA), is a kind of thermoplastic, which is widely used in engineering applications due to its excellent mechanical properties, good impact strength, high chemical resistance and wear resistance. Although it is easy to absorb and absorb moisture.
Nylon 6 and nylon 66 are the most commonly used grades in CNC machining.
Material properties:
Typical density: 1.14 g / cm3

Polycarbonate fiber
Polycarbonate is a thermoplastic with high toughness, good machinability and excellent impact strength (better than ABS). It can be colored, but it is usually optically transparent, so it is very suitable for a wide range of applications including fluid equipment or automotive glass.
Material properties:
Typical density: 1.20-1.22 g / cm3

POM(Delrin)
POM, whose commercial name is Delrin, is known as an engineering thermoplastic with the highest processability among plastics.
POM (Delrin) is usually the best choice when CNC machining plastic parts with high precision, high stiffness, low friction, excellent dimensional stability at high temperature and very low water absorption.
Material properties:
Typical density: 1.40-1.42 g / cm3

PTFE (Teflon)
PTFE, commonly known as Teflon, is an engineering thermoplastic with excellent chemical and heat resistance and the lowest coefficient of friction in any known solid.
PTFE (polytetrafluoroethylene) is one of the few plastics that can withstand temperatures above 200 OC and is an excellent electrical insulator. However, it has pure mechanical properties and is usually used as a lining or insert in an assembly.
Material properties:
Typical density: 2.2 g / cm3

High density polyethylene
High density polyethylene (HDPE) is a kind of thermoplastic with high strength to weight ratio, high impact strength and good weather resistance.
HDPE is a lightweight thermoplastic, suitable for outdoor use and pipeline transportation. Like ABS, it is often used to create prototypes before injection molding.
Material properties:
Typical density: 0.93-0.97 g / cm3

PEEK
Peek is a high performance engineering thermoplastic with excellent mechanical properties, thermal stability over a wide temperature range and excellent resistance to most chemicals.
Peek is often used to replace metal parts because of its high weight to weight ratio. It also provides a medical level that makes peek suitable for biomedical applications.
Material properties:
Typical density: 1.32 g / cm3

Rule summary
Aluminum 6061 is the most common CNC machining material with the lowest cost.
Due to its excellent processability, POM (Delrin) is the most economical CNC plastic.
Select a metal alloy for applications requiring high strength, hardness and / or heat resistance.
Choose plastics with special material requirements for lightweight applications or pre-injection prototypes.
Application range of various materials
Aluminum
Key performance: aluminum is highly valued for its strength to weight ratio and corrosion resistance. It also has good thermal conductivity and conductivity.
Aluminum 6061-t6:6061 is one of the most commonly used aluminum varieties and has been widely used. The T6 mark gives the material an ultimate tensile strength of 276 MPa. Common application: General
Aluminum 7075: ultimate tensile strength is 572 MPa, comparable to steel. Useful for high stress applications, its use is limited by high costs. Common applications: aerospace, automobile, ship
Aluminum 2024-T3: 2024-T3 2000 series alloy has high strength weight ratio, tensile strength is 400-430 MPa, yield strength is at least 270-280 MPa. T3 certification, solution heat treatment and cold working have been carried out. Common applications: industrial, aerospace, medical, electronic products.
Aluminum 5052: at 117 MPa, the fatigue strength of this kind of aluminum alloy is higher than that of most aluminum alloys. It also has excellent seawater and salt spray resistance. Common applications: ship, aerospace, electronics.
Aluminum mic-6: similar to 7000 series aluminum alloy, mic-6 is a cast plate material commonly used in mold and substrate. Common applications: aerospace, electronics, gear.

Brass, bronze and copper
Key features: pure copper is a soft and malleable metal with high thermal and electrical conductivity. Brass and bronze are alloys of copper. Brass is a mixture of copper and zinc, and bronze is mainly copper and tin. In general, brass is valued for its machinability and high strength retention. Bronze has low friction performance and high corrosion resistance. Brass, bronze and copper are usually chosen for aesthetic purposes.
C360 brass: C360 is a highly machinable material with the lowest cost of all brass alloys. Industry: industry, business.
Brass 260: the most malleable brass alloy 260 is used more than other similar products. Industry: industry, commerce.
C932 M07 bearing bronze: for light duty applications, this alloy is easy to process and corrosion resistant. Industry: general.
ETP copper C110: this alloy has the highest electrical conductivity (100% IACS) of all metals except silver (105% IACS). Industry: power, construction, medical.
Copper 101: base material for many brass and bronze, copper 101 has high ductility (elongation 5% to 50%) and impact strength. Industry: electronics, automobile.
Steel
Key features: can be said to provide the widest range of CNC machining materials, steel has stainless steel, alloy, tools and low carbon steel options. In general, steel has good mechanical properties and is easy to process.
Steel 1018: this low carbon general purpose steel is ductile and suitable for forming and welding. Industry: general, gear, screw, nut.
ASTM A36: an example of low carbon steel, A36 is a low-cost alloy with good mechanical properties, including ultimate tensile strength of 400-550 MPa and elongation at break of 20%. Industry: gear, construction.
Alloy steel 4130: this multifunctional steel alloy is optimized in terms of composition (strength limit (670 MPa), toughness (yield strength 435 MPa), and machinability). Industry: aerospace, oil and gas, automotive.
Stainless steel 304: the most common stainless steel variety and representative of the basic quality of steel, the alloy has higher corrosion resistance and lower conductivity than most other steels. It is not suitable for applications requiring welding. Industry: food, screw, automobile.
Stainless steel 17-4: this precipitation hardening stainless steel is known for its high strength and mechanical properties and can be further developed by heat treatment. It has good mechanical properties even at 600 degrees Fahrenheit, and has high corrosion resistance. This material can work well in harsh environments. Industry: nuclear, marine, food and medical.
Titanium
Key features: Although titanium is heavier than aluminum (but still lighter than steel), titanium is also known for its excellent weight to strength ratio. Due to their hardness, many titanium varieties are considered difficult to process.
Titanium grade 2: Grade 2 is a common form of this metal with high strength (limit 344 MPa) and excellent corrosion resistance. It is usually used to make heat exchangers. Industry: aerospace, automotive, chemical.
Titanium 6Al-4V: another commonly used titanium variety, this alloy is the best choice when low density (4.429 – 4.512 g / cm3) and excellent corrosion resistance are required. Industry: medical, aerospace, marine, natural gas.

Zinc alloy
Key feature: zinc is not commonly used in CNC machining because most varieties are too brittle for processing. In some specific forms, the material becomes easy to process and easy to handle.
Zinc alloy plate 500: a continuously cast alloy with Machinable zinc having good electrical conductivity and high corrosion resistance. Industry: architecture.
Plastic Material
Key features: lightweight and rugged, some industrial plastics can be considered as low-cost alternatives to metal parts. Plastics are widely used in all industries.
Abs: this common high-strength thermoplastic with electrical insulation is ideal for low-cost, lightweight molds and prototypes. Industry: general, medical, automotive, electronics.
Acetal: Delrin is the easiest plastic to process. It has excellent stiffness (bending strength 82.7 MPa), low friction and good moisture resistance. Industry: general, gear, electronics, medical, construction.
Nylon 6 / 6: common polyamide, nylon 6 / 6 (or 66 for short) has high mechanical strength (66 MPa), stiffness and stability under thermal and chemical action. Industry: automobile, electronics, gear, pipe.
Peek: this advanced thermoplastic can be used in all kinds of occasions with high mechanical requirements. Industry: medical, aerospace, automotive, electronics.
Polycarbonate: commonly known as PC, this transparent plastic has excellent optical properties. It’s rugged, lightweight and rugged with high impact resistance (600 – 850 J / M). Industry: general, electronics, aviation, automobile, pipeline.
Finishing services
Finishing service after machined can change the appearance, surface roughness, hardness and chemical resistance of the parts produced. The following is a brief overview of the most common surface treatments for CNC machining.
Machined
The machined parts have the most stringent tolerances because no additional work is required on them. However, the marking along the cutting tool path is visible. The standard surface roughness of machined parts is 3.2 μ m (125 μ in), which can be reduced to 0.4 μ m (16 μ in) by further operation.
The most stringent dimensional tolerance.
No additional cost (standard surface treatment).

Bead blasting
Bead blasting adds a uniform matte or satin finish to the machined parts, eliminating all tool marks.
Bead blasting is mainly used for aesthetic purposes because the surface roughness obtained cannot be guaranteed. Key surfaces or features such as holes can be masked to avoid dimensional changes.
A pleasing matte or satin finish.
Low cost surface treatment.
Provide different roughness.

Anodizing (transparent or colored)
Anodizing adds a thin and hard non-conductive ceramic coating on the surface of aluminum parts to improve their corrosion resistance and wear resistance.
Critical areas can be masked to maintain strict tolerances. Anodized parts can be dyed to produce a smooth, beautiful surface.
Durable, beautiful appearance.
Can be applied to the lumen.
Can be colored to any Pantone hue.

Hard coating anodizing
Anodizing of hard coatings produces thick, high-density ceramic coatings that provide excellent corrosion and wear resistance.
Hard coating anodizing is suitable for functional applications. A typical coating thickness of 50 μ m is not normally applied. Critical areas can be masked to maintain strict tolerances.
High wear resistant coating for high-end engineering applications.
Can be applied to the lumen.
Good dimensional control.

powder coating
Powder coating adds a layer of strong, wear-resistant and corrosion-resistant protective polymer coating on the surface of parts.
It can be applied to parts of any material and has a variety of colors to choose from.
Robust, wear-resistant and corrosive coatings for functional applications.
It has higher impact resistance than anodizing.
Compatible with all metal materials.

Silk screen printing
Screen printing is a cheap way to print text or logo on the surface of CNC machining parts for aesthetic purposes.
It can be used in addition to other finishes such as anodizing. Only the printed content can be applied to the outer surface of the part.
Print custom text or logo at low cost.
Available in a variety of colors.

Tips for reducing the budget of your CNC project
The cost of CNC machining parts depends on the following factors:
Processing time and model complexity: the more complex the geometry of the part, the longer the processing time and the higher the cost.
Start up costs: These are related to CAD file preparation and process planning, but the cost is basically fixed. There are opportunities to reduce unit prices through economies of scale.
Material cost and surface treatment: the cost of bulk materials and the ease of processing of materials greatly affect the total cost.
Let’s sum up
The 3-axis CNC milling machine can make parts with relatively simple geometry at low cost and have excellent accuracy.
The unit cost of CNC lathe is the lowest, but it is only suitable for parts with rotational symmetry.
The parts made by 5-axis CNC milling machine with index have the characteristics that they can’t align with one of the main shafts quickly and have high precision.
The parts manufactured by continuous 5-axis CNC milling machine have highly complex “organic” geometry and smooth contour, but the cost is high.
Milling CNC center combines the advantages of CNC turning and CNC milling into one system to manufacture complex parts at lower cost than other 5-axis CNC systems.

CNC machining parts are widely used in all walks of life. At ddprototype, we serve a wide range of areas, including:
medical care
automobile
Bicycle
robot
Aerospace
ship
agricultural machinery
electronic product
Camera and other precision manufacturing parts of all walks of life