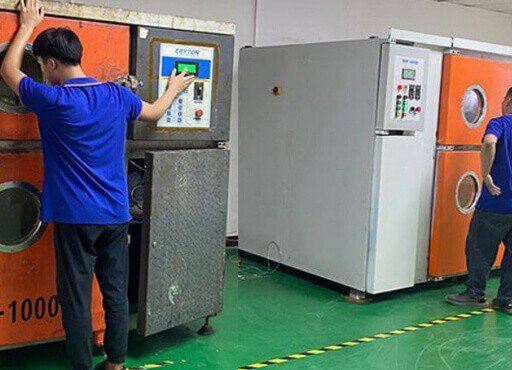
Rapid Prototyping & Rapid Manufacturing Expert
Specialize in CNC machining, 3D printing, urethane casting, rapid tooling, injection molding, metal casting, sheet metal and extrusion
Common plastic forming process vacuum casting
There are many forming processes for plastic parts, including injection molding, blow-molding, extrusion molding, blister molding, vacuum casting etc. Each plastic forming processing has its unique advantages and disadvantages. Today we will focus on introducing you the working procedure, advantages and disadvantages of the vacuum casting processing, as well as common material used for vacuum casting, etc.
What is vacuum casting?
Vacuum casting be called Urethane casting or Polyurethane casting also, is a process for making replicas of plastic parts and is one of the most economical processes for plastic parts forming in a small batches. Generally, will create a master through 3D printing or CNC machining first, and then use the master to make a silicone mold or rubber mold (Currently, most is silicone mold), inject liquid resin into the mold under vacuum circumstances and let it harden manufacturing method. Duplicate plastic parts can accurately replicate the structure, details and texture of the master and provide a consistent surface finish to obtain results similar to injection molding production. It is suitable for small batch trial production in the product research and development phase, with complex structure, uniform wall thickness, and trial production samples that meet certain functional requirements.

Processing steps of vacuum casting
The vacuum casting process manufacturing process is divided into three steps: making master, making silicone molds and casting parts.
Step 1: Make a Master
The quality of the duplicate parts depends on the quality of the master, and when you need to maintain high precision, high finish or even optical clarity, its better use CNC machining to create the master. In addition, for the parts with complex shapes and structures, we will consider using 3D printing to make the master as well. We can spray texture or matte effect on the surface of the master to simulate the final mold texture of the plastic parts. The silicone mold will reproduce the detailed and texture of the master accurately, and the surface of final replica will maintain a high degree of consistency with master.

Step 2: Make the Silicone Mold
The casting mold is made of liquid silicone, also known as RTV mold. Silicone rubber is chemically stable, self-releasing and flexible, minimizing shrinkage and efficiently replicating part details from master to mold. The manufacturing steps of the silicone mold are as follows:
Tape around the masteron a flat area for easy demoulding later, which will also be the parting surface of the silicone mold.
Hang the master in a box and place a glue stick on the partsto set the gating and venting hole.
Fill the box with liquid silicone and vacuum it, then cure it in an oven at 40°C for 8-16 hours, whichdepending on the size of the silicone mold.
After the silicone rubber is cured, remove the box and the glue stick, take the masterout of the silicone mold, then form a cavity, and the silicone mold is created.

Step 3: Vacuum casting
DD Prototype’s standardized operating procedures ensure accurate part reproduction and consistent mechanical performance. Our technicians control all operating parameters: mixing, venting, agitation, preheating, casting and demoulding, providing near-perfect replicas of master. The process of vacuum casting is as follows:
First put the silicone mold into the oven and preheat to 60-70℃.
Selecting a suitable release agent and using it correctly before closing the mold is very important to avoid sticking and surface defects.
To prepare polyurethane resin, preheat it to about 40°C before use, mix the two-component resin in the correct ratio, then fully stir and degas under vacuum for 50-60 seconds.
The resin is poured into the mold inside the vacuum chamber and the mold is cured again in the oven. Average curing time: 1-3 hours for small pieces, 3-6 hours for large pieces.
Remove castingparts from silicone mold after curing. Repeat this procedure.

Advantages of vacuum complex molding
Low cost of the molding, vacuum casting processing does not need to invest in expensive and time-consuming injection molds.
Quick turnaround, as many as 50 prototypes with certain functions can be produced within 10 to 15 days.
A wide range of material options, polyurethane materials for vacuum injection can be rigid, elastic, transparent, and various colors.
High precision and fine details. Vacuum castingcan provide high-precision and high-precision parts with production-level quality.
Excellent surface finish, compared with CNC prototype or 3D printing, vacuum castingmold provide better surface quality.

Common materials used in vacuum casting
Materials used in vacuum casting include thermoplastics, rubber and resins, all of which can simulate specific properties and characteristics:
Appearance quality
Surface texture/finish
Transparency/Translucency
Rigidity
Flexibility
Strength
Hardness
Temperature resistance
UV rays
Color
More FAQ about vacuum casting
What is the accuracy of the duplicated plastic parts created by vacuum casting processing?
-The standard replication accuracy tolerance is ±0.15mm/100mm, and the highest accuracy can reach ±0.05mm.
What is the maximum casting workpiece size?
-Vacuum casting equipment can accommodate 2.0M*1.2M*1.0M mold specifications.
What is the minimum wall thickness of plastic parts that can be reproduced?
-The minimum wall thickness of the part is 0.5mm, and the best is 1.5mm~2.5mm.
What is the service life of the silicone mold?
-Each mold can casting up to 20 pieces, and if the part requires high quality (such as transparent or complex structure), one mold can only make 12 or even 10 plastic parts..
What is the general delivery time for vacuum injection molding?
-Up to 50 cast prototypes can be made within 10 to 15 days, depending on part size and volume.
Surface treatment and other functions?
– Coloring of the liquid resin, matte etching, transparent polishing, painting, electroplating, metal inserts, overmolding, etc.
Vacuum casting processing is an effective method for manufacturing functional prototypes and small batches of plastic parts, and helps you balance high-quality production of plastic parts with the shortest lead times. If you would like to know how prototyping can benefit your project, please get in touch with DD Prototype, we want to hear you about your projects.