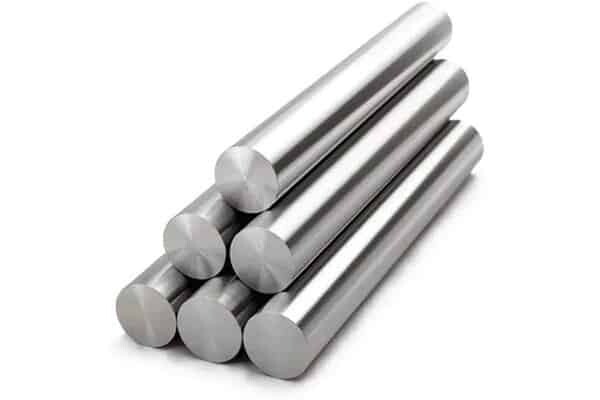
Rapid Prototyping & Rapid Manufacturing Expert
Specialize in CNC machining, 3D printing, urethane casting, rapid tooling, injection molding, metal casting, sheet metal and extrusion
Titanium VS Aluminum, For CNC machining Project
When choosing a lightweight yet high-strength material for your CNC machining project, titanium and aluminum should be the first things that come to mind. The same is true, both titanium and aluminum have excellent strength-to-weight ratios, are resistant to corrosion and heat, and have proven to be impressively versatile for custom parts or prototypes across various industries. To help you make the choice you want, we’ll do a comprehensive comparison of the differences between titanium and aluminum.
What is titanium?
Titanium is a strong, lightweight metallic material with a silvery sheen, high strength, good thermal conductivity and good corrosion resistance. Unfortunately titanium is difficult to purify and CNC mill, CNC turn, making it more expensive than many other metals. Titanium is stronger than ordinary mild steel and twice as strong as weak aluminum alloys, yet weighs 45% less than mild steel and 60% heavier than aluminum. Because titanium is stronger, less titanium is needed per unit strength. The melting point of titanium is 1668°C, and its atomic radius is 147 microns. It has strong alloying ability with iron, vanadium, molybdenum and other metals. Titanium is also non-magnetic and non-toxic, is a poor conductor of electricity, and has a low rate of thermal expansion. High biocompatibility is also a distinguishing feature of titanium, meaning it makes an excellent material for medical devices such as knee replacements, pacemakers, skull plates, dental implants and more. In addition, titanium has a high degree of corrosion resistance, making it widely used in chemical and marine applications.

In most cases, titanium is used in various fields in the form of titanium alloys. Titanium alloys are metals that contain a mixture of titanium and other chemical elements. This titanium alloy has very high tensile strength, toughness, light weight, excellent corrosion resistance and the ability to withstand extreme temperatures.
Grade 2 titanium alloy
Grade 2 titanium alloy. Grade 2 titanium alloys have excellent cold formability, weldability and have excellent resistance to oxidation and corrosion. Grade 2 titanium alloys are the preferred choice for many applications including aerospace, automotive, chemical processing and chlorate manufacturing, desalination and more.

Grade 5 - Ti-6Al-4V.
Grade 5 – Ti-6Al-4V. Grade 5 is the most commonly used titanium alloy, accounting for more than 50% of the global titanium consumption. It is an α+β alloy consisting of 6% aluminum, 4% vanadium, 0.25% (maximum) iron, 0.2% (maximum) oxygen , About 90% titanium composition. Since Ti-6Al-4V can be heat-treated, its strength, corrosion resistance, weldability and machinability are superior to commercial pure titanium (grade 1-4), and it can be applied in an environment of 400 degrees Celsius. Ti-6Al-4V is widely used in various fields, including: aircraft turbines, engine components, aircraft structural components, aerospace fasteners, high-performance automation parts, marine, etc.

What is Aluminum?
Aluminum is a reliable, strong, non-magnetic and ductile lightweight metal with a good weight-to-strength ratio, good corrosion resistance and high fracture toughness. Aluminum has a silvery-white appearance because it is exposed to the external environment and forms a thin layer of aluminum oxide on the surface to resist further corrosion. Aluminum is an inexpensive and easily CNC machined metallic material that is naturally resistant to acidic environments and corrodes easily in alkaline environments. Aluminum is more abundant in the earth than titanium in total and is easy to purify, so it is an economical choice.
Aluminum has a very good thermal conductivity, three times that of stainless steel, and is non-toxic. Its melting point is 660 degrees Celsius, making it an ideal choice for cooking utensils. It is usually widely used in various fields in the form of aluminum alloy, and its alloy elements are not limited to Cu, Mn, Si, Mg, Mg+Si, Zn. According to the ratio of alloying elements, aluminum alloys are divided into 9 series (Al1xxx to Al9xxx).

1xxx: No alloying elements
2xxx: Copper
3xxx: manganese
4xxx: silicon
5xxx: Magnesium
6xxx: magnesium and silicon
7xxx: zinc, magnesium and copper
8xxx: Other elements not covered by other series
Aluminum alloys are widely used in aerospace, automotive, construction, food processing, packaging, electrical and electronic fields, such as aircraft fuselages, engines, automotive wheels, radiators, cylinder blocks, crankshafts and other parts.
Difference Between Titanium and Aluminum
Comprehensively compare the difference between titanium alloy and aluminum alloy, find out the difference between titanium and aluminum, we can more easily choose the best material for your CNC machining project.
Elemental composition.The composition of alloying elements is very important, which affects certain properties of titanium or aluminum alloys, including corrosion resistance, high temperature resistance, weight, etc. Other elements of titanium alloys include nitrogen, hydrogen, oxygen, carbon, iron, and nickel, among others, in amounts between 0.013 and 0.5%. Other elements of aluminum alloys include silicon, zinc, magnesium, manganese, copper, iron, titanium, chromium, zirconium, and the like.
Corrosion resistance.Both titanium and aluminum have excellent corrosion resistance, but titanium is generally considered to be more corrosion resistant than aluminum due to titanium’s inertness. Titanium is also highly biocompatible and has more applications in the medical industry. Also, titanium’s corrosion resistance in seawater is impressive, making it very popular in the marine industry as well. On the other hand, a layer of oxide film will be formed on the surface of aluminum alloy, so it is not easy to chemically react with corrosive materials, but it also depends on the chemical substances, temperature and other factors in the environment. When a CNC machining project has corrosion resistance as a primary consideration, titanium is the ideal choice.
Usually, we use copper as the standard for conducting electricity, and its conductivity is 100%. Titanium has a conductivity of 3.1% of copper, so titanium is not a good conductor of electricity, but it can be used to make resistors. Aluminum has a conductivity of 64% that of copper, so aluminum is a good conductor of electricity. Aluminum is ideal if electrical conductivity is a top concern for your CNC machining project.
Thermal conductivity.The thermal conductivity of a material is very important for making heat-dissipating parts or prototypes. Titanium has a thermal conductivity of 118 BTU-in/hr-ft²-°Fm (17.0 W/mK), while aluminum has a thermal conductivity of 1460 BTU-in/hr-ft²-°F (210 W/mK) ten times. This is why aluminum is often used to make radiators, heat exchangers, kitchen appliances.
Melting point.The temperature at which a metal changes from solid to liquid is called its melting point. At the melting point, metals belong to an equilibrium state of solid and liquid. Metals with lower melting points are usually easier to mold for injection molding or extrusion. Titanium has a melting point between 1650 – 1670 °C, which is a very high temperature. Aluminum, on the other hand, has a melting point of 660.37 °C. If heat resistance is a top concern for your CNC machining project, titanium is the ideal material.
The hardness of the material is generally referred to the Brinell hardness value, the Brinell hardness of titanium is 70 HB, and the Brinell hardness of pure aluminum is 15 HB, but the hardness of some aluminum alloys such as 7075 and 6082 is higher than that of titanium. Titanium forms a very hard titanium oxide layer on the surface, ideal for CNC machining projects where hardness is the primary factor.
The density of titanium is 4500 kg/m 3 , while the density of aluminum is 2712 kg/m 3 , so per unit volume, titanium is 60% heavier than aluminum. Under the same physical strength, less titanium will be used. If strength-to-weight ratio is a primary consideration for your CNC machining project, titanium is preferable to aluminum. Aluminum is more suitable if light weight is the primary factor.
Both titanium and aluminum are very durable and will work for a long time. Titanium is extremely strong, such as eyeglass frames made of titanium, can be used for decades without wear and tear. Both titanium and aluminum are suitable for making custom parts or prototypes for durability. If the two are compared, titanium is more durable.
Machinability The degree to which a metal responds to machining stress, including stamping, CNC turning, CNC milling, etc. CNC machining is ideal for manufacturing titanium or aluminum parts, typically within 24 hours and within +/- 0.005 inches (0.13mm). But CNC machining titanium parts is often challenging due to the build-up of titanium swarf on the high-speed rotating tool. CNC machining aluminum is very easy, which is why the cost of CNC machining aluminum is usually much lower than that of titanium.
The price of titanium alloy is higher than that of aluminum alloy. Of course, CNC machining titanium is more difficult and costly, and grinding, bending, and welding titanium requires more professional knowledge. Aluminum is relatively more cost-effective.
Yield strength. Yield strength refers to the stress at which a material permanently deforms. Titanium has a yield strength of 170 MPa to about 480 MPa, while pure aluminum has a yield strength of 7 MPa to about 11 MPa. The yield strength of aluminum alloys is between 200 MPa and 600 MPa.
Tensile strength.The strongest tensile strength of titanium alloy is about 1400 MPa, while that of aluminum alloy is above 690 MPa.
Application of titanium alloy
Titanium alloys are used in a wide range of applications, including:
Aerospace industry – used to manufacture aircraft landing gear, hydraulic systems, other critical structural components, etc.
Medical Industry – Manufacture of products such as dental implants, hip replacements, knee replacements, surgical instruments, etc.
Consumer and Construction – Manufacture of sporting goods, eyeglass frames, bicycle (mountain bike, race car, etc.) parts, firearms, etc.
Industrial Applications – Manufacture of valves, heat exchangers, sputtering targets, process vessels, etc.
Marine and Aerospace (landing gear, firewalls, critical structural components, hydraulic systems.
Jewelry (watches, rings, necklaces, etc.).
Application of aluminum alloy
Power systems – conductor alloys, generators, motor transformers, etc.
Consumer goods – household items such as cooking utensils and furniture.
Machinery and equipment – tools, pipes and other work materials.
Transportation (airplanes, railcars, bicycles, cars, trucks, ships, spacecraft, etc.)
Packaging (cans, frames, foil)
Building and construction (windows, siding, roofs, doors, building wiring, sheathing, etc.)
Should you use titanium or aluminum?
Titanium and aluminum are two important metallic materials for the manufacture of CNC custom parts and prototypes, and their properties make them a versatile choice for many different industry applications. This article compares the different properties of titanium and aluminum, please consider various factors between choosing the two materials. For more help, DDPROTOTYPE is always ready to provide constructive information.
Correct our misconceptions
Myth: “Titanium is much lighter than aluminum.”
Sorry, this opinion is incorrect, when we look at the material density, Titanium’s 4.5 g/cc density is actually 50% heavier than Aluminum’s 3.0 g/cc.
Myth: “Titanium is stronger than aluminum.”
It depends on the alloy type, but 7075-T6 aluminum has almost twice the strength-to-weight ratio of grade 2 titanium.
Myth: “Aluminum is bad for the environment”
Titanium emits more than 3 times the amount of carbon dioxide than aluminum during material manufacturing, transportation and construction.
Myth: “Aluminum is harmful to humans.”
This is unreliable information that has been circulated since the 60’s. In fact, 60 percent of the pots and pans sold in the U.S. each year are made of aluminum, and the FDA reports that the amount of aluminum that enters food is significantly lower than the amount naturally found in food. Plus, hard-anodized aluminum adds an ultra-tough, durable finish to the pristine finish for better looks and safety.