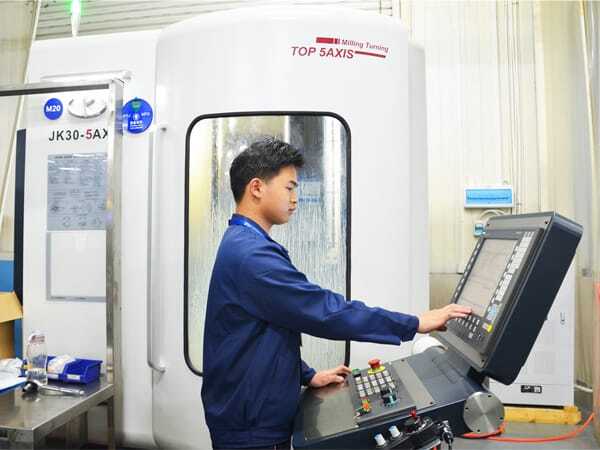
Rapid Prototyping & Rapid Manufacturing Expert
Specialize in CNC machining, 3D printing, urethane casting, rapid tooling, injection molding, metal casting, sheet metal and extrusion
Everything You Should Know About CNC Machining Medical Parts
The medical device industry is an industry that does not allow mistakes. Any improper operation will affect people’s lives and health. It involves vast production lines ranging from surgical knives to artificial joints to large diagnostic equipment, requiring precise dimensions, real materials and specified surface treatments. With the advantages of tight tolerances, excellent surface finish, and compatibility with hundreds of materials, CNC machining is one of the ideal machining processes for custom machined medical parts.
Advantages of CNC machining medical parts
CNC machining is a general purpose subtractive manufacturing process in which manufactured medical parts or assemblies are cut from materials. The technology is so advanced that the computer-aided design (CAD) file guides the CNC machine tool along the correct path, replaces the tool, and cuts the material precisely to produce excellent medical equipment, tools and parts, which are widely used in surgery, dental equipment, diagnostic equipment, etc.

Fast. Compared with injection molding, CNC machining does not require additional molds, only some machine settings, and the conversion of CAD files to G-code. The CNC machine tool starts the cutting program quickly according to the instruction, and usually can manufacture complex parts within a few hours. Molds, on the other hand, take weeks or even months. Medical testing is usually more urgent. For example, the current COVID-19 is raging around the world, and the demand for testing equipment has surged. CNC machining can provide high-quality medical parts or prototypes in a short period of time for products to go to market as soon as possible.
No quantity limit. During the machining process, the CNC machine tool can identify whether to process one part or to manufacture multiple parts. Compared with other manufacturing processes, the cost of manufacturing a part is much smaller. The production of one-off or individual custom parts is common in the medical world, such as specialized medical devices, appliances and other medical components. CNC machining is very advantageous. For example: Different human body structures require different medical aids, which is why CNC machining is one of the reasons for manufacturing prosthetics, and there is no minimum order quantity requirement.
Compatible with various materials. Whether it is high-strength, high-toughness stainless steel, titanium alloy, aluminum alloy, or even nickel-molybdenum alloy, or engineering plastics PEEK, Teflon, etc., CNC processing can be perfectly compatible, and hundreds of materials can be selected to manufacture medical parts or prototype. Compared with 3D printing, the choice of materials is wider.
Tight tolerances. Usually, medical equipment or parts require strict tolerances, which is not difficult for CNC machining, especially 5-axis CNC machining can manufacture parts with a tolerance of 0.005mm, which meets the precision requirements of most medical parts , reducing the risk.
Excellent surface finish. Compared with 3D printing, parts manufactured by CNC processing usually have excellent surface finish, and there is almost no need to manually reprocess the surface of the part, which is very smooth.
The process of CNC machining medical parts
CNC milling. For added convenience, 5-axis CNC milling services are fully capable of making parts of any shape, often with the complex geometries that medical devices have. 5-axis CNC machining refers to 5-axis simultaneous machining, not 3+2 axes or 4+1 axes. Although many manufacturers boast of providing 5-axis CNC machining services, please confirm that they can provide real 5-axis simultaneous CNC machining services.

CNC Milling

CNC Turning
CNC turning. CNC turning can process parts with precise symmetry, such as shafts, round parts, etc. CNC turning processes include cutting, knurling, facing, forming, threading, broaching, drilling and boring.
CNC Swiss machining/micro machining. CNC Swiss Machining Lathes can rotate parts along 7, 9 or even 12+ axes to manufacture critical small medical parts such as needles, nails, bone screws, suture anchors, stents, clips, catheters and more in a fraction of the time. CNC Swiss machined medical parts to tight precise tolerances.
Quality inspection – three-coordinate inspection. Medical components or prototypes must undergo quality checks after processing. The CMM moves along the X, Y, and Z axes in a humidity/temperature-regulated laboratory, and detects the tolerances of medical parts through various visual or contact methods. It needs to fully meet the accuracy requirements of CAD models and 2D drawings, and meet reliability and safety requirements.
General CNC machining medical parts size limit
Currently, state-of-the-art CNC machining and other manufacturing technologies such as 3D printing and injection molding still have certain limitations. CNC machining of medical parts also has certain size limitations, not all medical parts require a tight tolerance of +/- 0.0001mm.
Forming and Bending: +/- 0.4mm
Bending: +/- 0.2mm
Linear Dimensions: +/- 0.1mm
Diameters with Inserts: +0.06mm / -0.0mm
Angularity: +/- 2°
Surface Roughness: Ra 100 uin max
Materials for CNC manufacturing of medical parts or prototypes
Medical materials must have a high degree of corrosion resistance and strength, and be easily sterilized and cleaned. The more common ones are stainless steel, titanium alloy, aluminum alloy, magnesium alloy, nickel-titanium alloy, etc. Based on more than 20 years of experience and practical exploration, DDPROTOTYPE, a top prototype manufacturer in China, summarizes the common materials suitable for CNC processing technology to manufacture medical parts, as follows.
Stainless steel 316/L.Stainless steel 316/L is highly corrosion resistant and is a commonly used material for medical devices.
Stainless steel 304.Stainless steel 304 has corrosion resistance and good machinability. It is one of the most widely used materials for manufacturing medical parts, but it cannot be heat treated. If a harder stainless steel is required, stainless steel 18-8 is more suitable.
Stainless steel 17-4. Stainless steel 17-4, commonly used in medical equipment, is a high-strength, corrosion-resistant stainless steel alloy that can be heat treated.
Titanium grade 2.Titanium Grade 2 is a high-purity, unalloyed titanium material that is high-strength, light-weight, and has high thermal conductivity.
Titanium grade 5.Such as Ti-6Al-4V, which has excellent strength-to-weight ratio, has good corrosion resistance, weldability and biocompatibility, flexibility, non-toxic, is one of the most common titanium alloys, and is widely manufactured for human implants Objects, such as artificial limbs, human joints, etc.
Nitinol ®: Nitinol is an alloy of titanium and nickel, which has been highly recognized by the medical community in recent years. It has memory, excellent damping coefficient, biocompatibility, and elasticity, and is very suitable for manufacturing various types of medical equipment.
Cobalt chromium alloy. Cobalt Chrome (Cobalt Chrome) is a high-strength metal alloy composed of cobalt and chromium. It is another biocompatible metal and has become one of the approved materials for dental and orthopedic implants.
Magnesium alloy.Magnesium alloy is a lightweight metal that is also biocompatible and widely used in the manufacture of cardiac stents.
Aluminum alloy.Aluminum alloys, such as aluminum 6061-T6, have become the main material for manufacturing various medical devices. They are strong, lightweight, corrosion-resistant and malleable. In addition, aluminum parts or prototypes are very economical and cost-effective. Anodized aluminum can further improve corrosion resistance, strength, and a variety of colors can improve aesthetics.
Other metal materials.Includes Brass, Bronze, Copper, Gamma, Hastelloy, Inconel, Invar, Manganese, Molybdenum, Monel, Nickel, Nitro, Platinum, Stellite, Waspaloy, Zinc and many more Other superalloys, etc.


Common medical plastic materials have moisture resistance and good thermal properties, and must also be sterilized by high temperature, gamma rays, or ethylene oxide. Compared with metals, plastics are not magnetic and do not interfere with diagnostic results and are commonly used in medical testing equipment.



Delrin.Delrin is a non-absorbent, wear-resistant and low coefficient of friction resin.
Polycarbonate (PC).PC has excellent mechanical and structural properties, with almost twice the tensile strength of ABS.
PEEK.Usually a substitute for metal parts, PEEK is corrosion-resistant, wear-resistant, has excellent tensile strength, and can work under high temperature and high pressure.
UHMWPE.UHMWPE has low friction coefficient, impact resistance, chemical resistance, and does not absorb water, so it is a general material.
PTFE (Teflon).PTFE can operate in extreme temperatures, has excellent chemical resistance, is an excellent insulator, and is one of the most widely used materials for making medical parts or prototypes.
Carolete G-10.Garolite G-10 is an alternative material for metal medical parts, has high strength and low water absorption, and is not magnetic.
Surface treatment process of CNC medical parts
Since medical parts or products are in close contact with the human body, the safest and environmental friendly surface treatment process is required.
Anodizing. Through electrolytic passivation, a thin layer of metal oxide can be formed on the surface of CNC machining medical parts to protect the metal and further improve corrosion resistance and wear resistance. There are various color options, as well as improve corrosion resistance and wear resistance. abrasion resistance. This process is most widely used on aluminum alloy medical parts. Stainless steel, copper, titanium, zinc alloys and magnesium alloys can also be anodized.

Anodizing

Passivation
Passivation.Passivation is often used on steel and stainless steel. The acidic solution removes free iron and ferrous iron from the surface, further enhancing the corrosion and chemical resistance of steel and stainless steel, preventing rust.
Electroplating. Plating, often nickel or chrome, forms a thin coating on the surface of the metal that adds thickness to tiny parts, prevents rust and improves corrosion resistance.
Polishing. The surface of medical parts is rubbed or chemically acted to make the surface extremely smooth and obtain a mirror effect.
Spray paint. Spray paint and pigments on the surface of medical parts to improve the aesthetics and avoid corrosion or oxidation. It is often applied to metal parts such as aluminum and stainless steel, as well as various engineering plastic parts.
Application of CNC machining medical equipment
Medical implants.CNC machining of parts for body implants is a major development in the medical field, such as hip replacements, hip implants, spinal implants, knee implants, and more. Commonly selected materials are: titanium alloy, cobalt-chromium alloy, stainless steel, PEEK, etc.
Surgical instruments. The high precision and flawless design of surgical instruments can make or break a procedure, sometimes requiring tighter tolerances such as +/- 0.002 mm. Common CNC-processed surgical instruments include: spacers, clips, pliers, knives, surgical scissors, piece handles, saws, tweezers, spacers, etc. The materials usually selected are: stainless steel, especially AISI 316L,Titanium alloy etc.
Electronic medical equipment.Many electronic medical devices are often composed of thousands of CNC-machined parts, including switches, buttons, electronic housings, and more. Some electronic medical devices include: heart rate monitors, MRI scanners and X-ray machines, ultrasound equipment, MRI scanners, CT scanners, diagnostic equipment, monitors, and more.
Certification of CNC Machining Shops
Manufacturing medical parts or prototypes is not the same as manufacturing parts for other industries. Mostly ordinary metal or plastic parts only need to follow the requirements of ISO 9001 quality management, but the manufacture of medical parts must also meet further standards. According to international standards, organizations involved in medical design, development, production, storage, distribution, installation or repair must demonstrate the ability to “provide medical devices and related services that consistently meet customer and applicable regulatory requirements.”
ISO 9001:ISO 9001 is applicable to various industries and is a general standard for quality control. It helps to minimize costs and promote company growth.
ISO 13485: This emphasizes the process supervision of CNC machining medical parts and standardizes the manufacturing process. The details of this standard are more stringent than ISO9001, such as process verification, risk management and quality control.
ISO 14001:Similar to ISO5001, it is a guideline that CNC machining of medical parts can reduce energy consumption and waste generation.
CNC machining is becoming more and more popular in the medical field. It is an ideal manufacturing process for manufacturing medical device parts with complex structures and hard materials. Especially, 5-axis simultaneous machining has made outstanding contributions to the manufacture of various orthopedic implants and dental implants.