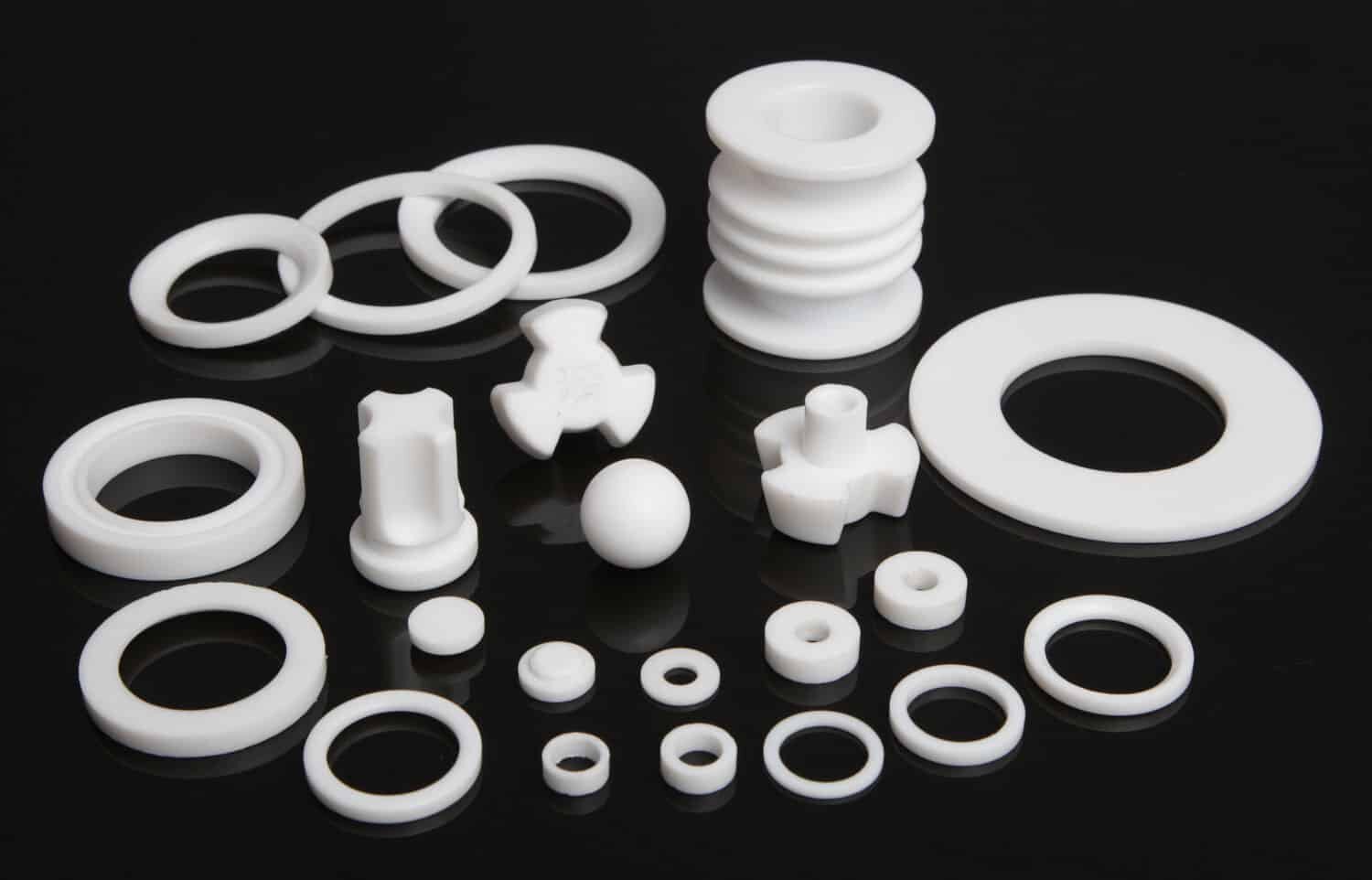
Rapid Prototyping & Rapid Manufacturing Expert
Specialize in CNC machining, 3D printing, urethane casting, rapid tooling, injection molding, metal casting, sheet metal and extrusion
What You Should Know About Machining Teflon
Polytetrafluoroethylene (PTFE), a polymer composed of carbon and fluorine atoms, it is an engineering thermoplastic, best known as DuPont’s Teflon. Teflon is the most high temperature resistant of all engineering plastics, with lots of advantages such as elasticity, corrosion resistance, abrasion resistance, chemical resistance, etc., making it ideal for making parts that require impact resistance and durability. In addition, it has a very low moisture absorption rate relative to nylon and can still work in wet environments, with applications ranging from consumer products to medical devices, aerospace components, and more.
What is Teflon?
Teflon is a white solid at room temperature, and melting point is 327°C. The bond composed of carbon and fluorine (one of the strongest bonds available in organic chemistry) with non-reactive character, and Medical implants made of Teflon will not be rejected by the body, and has a very low coefficient of friction, it is one of the ideal materials for making sliding parts such as bearings. Although the Teflon surface is relatively soft, it is difficult to maintain precision, CNC machining is still one of the best ways to make Teflon parts or prototypes. The CNC machining cost factor of PTFE/Teflon is 1.2 compared to steel 12L14.

At a glance
Processes | Lead Time | Tolerance | Price | Applications | Grades | Colors |
CNC Milling CNC Turning | As fast as 3 days | Following drawing: as low as +/- 0.005 mm No drawing: ISO 2768 medium | $$ | High rigidity and strength applications like gears, bushings, and fixtures | 150, AF (13% PTFE Filled), 30% Glass Filled | White, black, brown |
Mechanical properties of Teflon
– Density: 2.15 g/cm3
– Surface hardness: SD63
– Tensile Strength: 1,500 – 3,000 PSI (25 MPa)
– Flexural Modulus: 72,000 PSI (0.70 GPa)
– Water absorption (24 hours soaking): <0.01%
– Friction coefficient (dynamic): 0.10

Advantages of Teflon
Excellent chemical resistance
Excellent UV/weather resistance
waterproof; hydrophobic
High impact resistance
Good electrical insulator
Maintains mechanical properties between -260°C and 260°C
Non-stick, lubricated, low coefficient of friction
Flame retardancy
Food safety
Easy to clean
Limitations of CNC Machining Teflon
Has a high coefficient of expansion
Creep after stress
Difficulty controlling tight tolerances
Poor mechanical properties
Poor dimensional stability
During machining, it will haveburrs

Applications of Teflon
Medical and surgical equipment: grafts of tissues and organs, medical implants, etc.
Construction and decoration: the most common is paint.
Garment industry: raw materials for clothing.
Vehicles and cars: lightweight components.
Aerospace industry: coatings, cable insulation, hoses for fuel, etc.
Food processing: machinery and equipment for bakery and food.
Oil and gas: hoses and pipelines, PTFE potting caps, etc.
Power and electronics: insulator arc shielding, etc.
Components of machinery and various equipment: seals, gaskets, valves, fittings, pump parts, manifolds, semiconductor equipment, bearings, bushings, sliders, gaskets, mechanical gears, etc.
Tips for CNC Machining Teflon
After a lot of practice, DDPROTOTYPE, a top prototype manufacturer in China, can use CNC machining Teflon to achieve a tolerance of 0.1 mm.
– Due to Teflon’s high coefficient of expansion and stress creep properties, it is difficult to keep tight tolerances by CNC machining. The best surface finish and tight tolerances can be obtained by using non-aromatic water-soluble coolants during machining.
– Teflon is not recommended for unbalanced, bowl-shaped or disc-shaped components or parts.
– The thermal expansion of Teflon is several times of some metals, and the heat dissipation is slower. It is necessary to avoid local overheating during processing.
– Use a carbide tool with a smooth sharp edge to improve the surface finish.
– Clamp the workpiece well to avoid deflection.
– Keeps chips flowing and prevents clogging.
– Establish a deburring strategy in advance
The Teflon surface is non-stick, it is best to keep the part surface as machined, for a more uniform surface smoothness, sandblasting can be used.