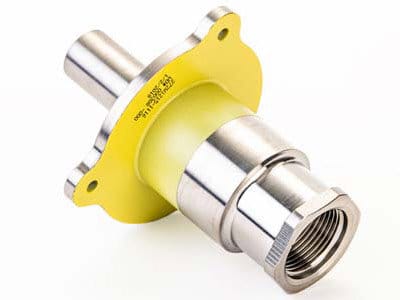
Rapid Prototyping & Rapid Manufacturing Expert
Specialize in CNC machining, 3D printing, urethane casting, rapid tooling, injection molding, metal casting, sheet metal and extrusion
Aluminum and stainless steel parts for aerospace
Aluminum and stainless steel parts for aerospace applications are the subject of our discussion. Aluminum used to make up most of the materials used in aerospace applications. However, aluminum accounts for only 20% of the materials used in today’s typical jets. Due to the demand for light aircraft, composite materials, carbon reinforced polymers and honeycomb materials are more and more popular in the aerospace industry. Other requirements, such as the ability to withstand high temperature and pressure, as well as corrosion resistance, differentiate other materials that were previously thought to be unsuitable for use in the aerospace industry.
Aluminium for Aerospace
Although the use of aluminum has declined in many aspects of aerospace production, it is still widely used in modern aircraft. For many specific purposes, aluminum remains the strongest and lightest material. Because of its high ductility, it is easier to process and relatively cheaper than many composites or titanium. It can also be further strengthened by alloying it with other metals, such as copper, magnesium, manganese and zinc, or by cold or heat treating it.
When aluminum is exposed to the air, the tight chemical oxide bond means that aluminum is isolated from the environment, making it highly resistant to corrosion. Aluminum can also be refined in many ways to adapt to the same wide range of applications. The high conductivity of aluminum makes it an ideal raw material for many applications.

The most popular aluminum alloys for aerospace parts manufacturing include:
Aluminum alloy 7075 (aluminum / zinc)
Aluminum alloy 7475-02 (aluminum / zinc / magnesium / silicon / chromium)
Aluminum alloy 6061 (aluminum / magnesium / silicon)
The choice of alloy depends entirely on the functional requirements of the end part.
Many of the aluminum components on the aircraft are only decorative, while other aluminum components have very high functions and require specific performance.



Learn more
In the past, aluminum has been widely used in the entire aerospace industry, but in recent years, the aerospace industry has broadened its horizons and began to rely on a wider range of materials. However, the advantages of aluminum alloy still make aluminum a major resource in the field of aerospace. Despite its greater weight, stainless steel has recently been found to be used in aerospace applications, especially for parts requiring high strength, corrosion resistance and heat resistance.
Stainless steel parts for aerospace applications
Stainless steel is an alloy made of an alloy made of steel and chromium. The strength of stainless steel is directly related to the content of chromium in the alloy. The higher the chromium content, the stronger the steel. Although stronger than aluminum, stainless steel is usually much heavier, which hinders its widespread use in aerospace applications. However, compared with aluminum, stainless steel parts have two main advantages:

Stainless steel has high corrosion resistance.
Stainless steel is stronger and more wear resistant. Compared with aluminum parts, stainless steel parts can better handle scratch / impact damage. The use of stainless steel alloys in aircraft components that require high strength but can cope with increased weight has been found to increase. Stainless steel has high corrosion and high temperature resistance, making it suitable for a series of aerospace components, including actuators, fasteners and landing gear components.

DDPROTOTYPE specializes in precision CNC machining of advanced materials for aerospace and most other industrial applications. Please contact us for more information on how we can meet your precision machining requirements for aluminum and stainless steel.