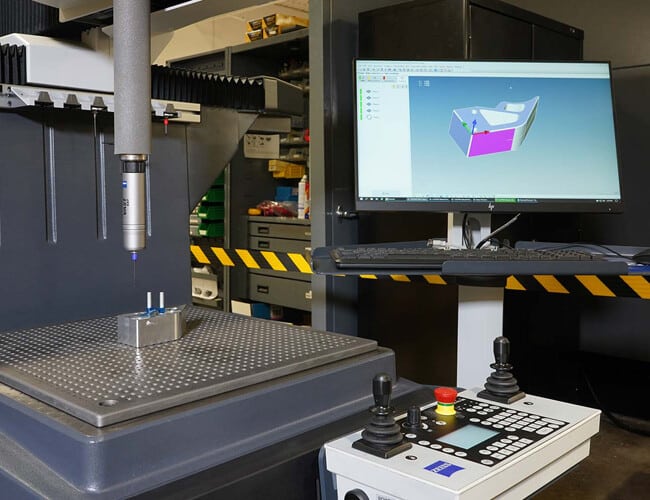
Rapid Prototyping & Rapid Manufacturing Expert
Specialize in CNC machining, 3D printing, urethane casting, rapid tooling, injection molding, metal casting, sheet metal and extrusion
Manufacturing Standards
DDPROTOTYPE manufacturing standards to help you optimize the design of the manufacturing method of your choice.Unless we agree with the other tolerances in your quote, we will strive to achieve and maintain the tolerances described below, which will vary depending on the main manufacturing method you choose.
CNC Machining
By default, sharp edges are destroyed and deburred. Care must be taken and specified on the print that the critical edge must be sharp.
Suitable for size (length, width, height, diameter) and position (position, concentricity, symmetry) +/- 0.005 “.
For directional (parallelism and perpendicularity) and shape (cylindrical, flatness, roundness, and straightness) features, the following tolerances apply:

Vacuum casting
Typical values are +/- 0.010 “or +/- 0.003” per inch, whichever is greater. Irregular or excessively thick geometries can cause deviations or deflections due to shrinkage.
Due to the thermal expansion of the liquid and the response of the flexible mold, a shrinkage rate of + 0.15% can be expected.
The surface finish is smooth on the outside to a satin or matte surface. Growth lines may exist on internal or hard-to-access features. Polished or custom finishes must be clearly defined and agreed upon when ordering.
We can provide polyurethane castings up to 30 inches.

SLA-Stereolithography
Tolerances for standard resolution:
X / Y plane: typically the first inch is +/- 0.005 “, and thereafter plus +/- 0.002” per inch.
Z-Plane: Typical first inch is +/- 0.010 “, and thereafter plus +/- 0.002” per inch.
Minimum linear feature size: Below 0.030 “at risk and below 0.020” will not be constructed.
Minimum radial feature size: 0.035 “
Tolerances are guaranteed through manual quote reviews and must be approved on a case-by-case basis.
High-resolution tolerances:
X / Y plane: typically the first inch is +/- 0.005 “, and thereafter plus +/- 0.002” per inch.
Z-Plane: Typical first inch is +/- 0.010 “, and thereafter plus +/- 0.002” per inch.
Minimum linear feature size: Below 0.020 “at risk, below 0.010” will not be constructed.
Minimum radial feature size: 0.030 “
Tolerances are guaranteed through manual quote reviews and must be approved on a case-by-case basis.
SLS-Selective Laser Sintering
A typical first inch is +/- 0.005 “, and thereafter plus +/- 0.002” per inch.
Parts with thicker geometries, flat or wide parts, and parts with uneven wall thickness will be prone to significant deviations or warping due to variable heat shrinkage and stress.
Tolerances are guaranteed through manual quote reviews and must be approved on a case-by-case basis.
Plastic Injection molding
The lead time mentioned is the first shipment. Confirm the remaining production time after approval of the first article.
A typical first shipment is 10 pieces.
Perfect color matching of Pantone colors cannot be completely guaranteed.
All quotes are based on the design’s core assumptions of adequate draught, radius and manufacturability.
Unless explicitly discussed, core, side effects, and tool strategies are determined by DDPROTOTYPE.
Unless otherwise stated, tolerances between manufactured parts and 3D CAD are +/- 0.010 “. Part-to-part repeatability is typically below 0.004”.
Unless explicitly discussed, gating, ejection, braiding and parting lines are at the discretion of DDPROTOTYPE.