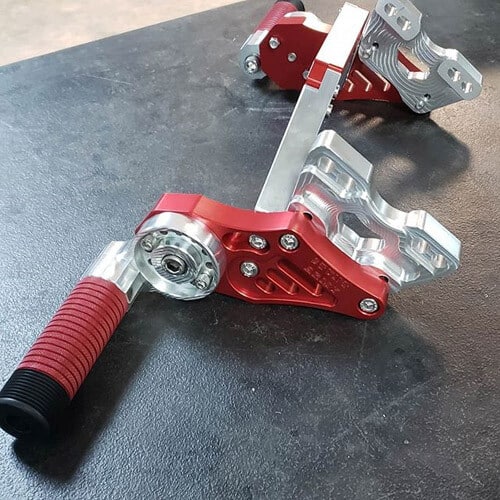
Rapid Prototyping & Rapid Manufacturing Expert
Specialize in CNC machining, 3D printing, urethane casting, rapid tooling, injection molding, metal casting, sheet metal and extrusion
Aluminum Anodizing
Anodizing is an electrochemical process that transforms metal surfaces into decorative, durable, corrosion-resistant, and oxidative treatments. Aluminum is well suited for anodizing, but other metals, such as magnesium and titanium, can also be anodized.
The anodic oxide structure is derived from an aluminum substrate and is composed entirely of alumina, a process that undergoes a chemical reaction. This alumina is not painted on the surface like paint or electroplating, but is fully bonded to the underlying aluminum substrate, so it does not crack or peel.
What is anodizing?
Anodization is accomplished by immersing aluminum in an acidic electrolyte and passing a current through the medium. The cathode is installed inside the anodizing tank; aluminum functions as an anode, allowing oxygen ions to be released from the electrolyte and combined with aluminum atoms on the surface of the anodized part. Therefore, anodic oxidation is a highly controlled chemical reaction phenomenon.

For Various Industries
Anodizing is one of the surface treatment methods for prototype parts, especially for aluminum prototypes, but also for magnesium and titanium prototype parts. Of course, DDPROTOTYPE can provide anodized aluminum hard coating services, transparent, black, gray, red, blue, gold. Custom anodizing services for hard coatings can be used in a wide range of areas. Various industries benefit from the use of anodized aluminum parts, including: automotive, aerospace, construction and construction, electronics, food manufacturing equipment, household, marine industry, medical / dental, equipment, sporting goods, etc.


Design considerations
The thickness of the anodized coating is 0.0002-0.0012 “, which conforms to the general engineering specification MIL-A-8625 Type II.
-Parts without holes are suspended from the conductive frame, which can leave a small area without anodizing treatment, called a “rack mark”.
-Anodizing has insulating properties, so anodized parts provide poor conductivity.
-Anodized parts up to 2438 x 762 x 1219 mm (96 x 30 x 48 in)

Custom aluminum anodizing service for your project
Aluminum hard anodizing, also known as MIL-A-8625 Type III or engineering anodizing, is similar to standard anodizing because they are all controlled electrochemical processes. Hard anodizing is usually transparent or uses black-dyed coatings, although some engineers prefer aluminum to a different color for aesthetic appearance. DDPROTOTYPE provides color anodizing services, as well as customized services for hard coating transparent anodizing.
Over time, aluminum naturally forms an oxidized surface. However, our Type III custom anodizing service provides a more uniform, dense and harder surface than natural anodized surfaces in a fast and efficient process.
DDPROTOTYPE’s factory in Shenzhen, China, provides anodized aluminum hard coating services (type III) and clear anodized aluminum services for dyed and non-dyed parts. We also provide standard aluminum anodizing (type II) services. Contact us today for a competitive aluminum anodizing service quote.
Hard coating color anodizing service
Depending on the alloy and coating thickness, DDPROTOTYPE color anodizing services are available in a variety of colors. In order to provide the best color coating selection, if colors other than black are required, DDPROTOTYPE needs sampling. For example, the color of hard-coated anodized aluminum depends on the thickness of the alloy and coating. On some alloys, the color of undyed (MIL-A-8625 Type III Class I) aluminum changes to gray / bronze after hard anodizing; black is the most commonly used color.

Benefits of hard anodizing
DDPROTOTYPE hard-coated aluminum anodizing service can be applied to various aluminum prototype parts. The aluminum hard coating improves the overall aesthetics of aluminum while increasing strength and corrosion resistance.
-Easier to clean and maintain
-Improved lubrication
-Resistant to peeling, flaking and chipping
-Improve abrasion resistance
-Flame retardant
-No pollution (for medical instruments)

Impact on tolerance
Type III anodizing must take additional care to ensure that parts remain within specified tolerances. Even the thinnest type III can affect the tolerance of the reaming hole, making the threaded hole inoperable, etc. Because the protective oxide layer must be thicker than 0.001 “and sometimes coated up to 0.004”.