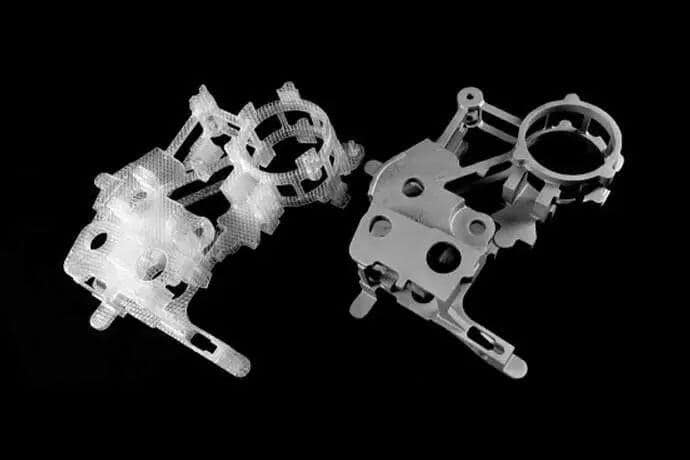
Rapid Prototyping & Rapid Manufacturing Expert
Specialize in CNC machining, 3D printing, urethane casting, rapid tooling, injection molding, metal casting, sheet metal and extrusion
Material guide for manufacturing plastic prototypes
When manufacturing plastic prototypes, it seems difficult to select more suitable materials, especially considering the need for mass production of plastic parts. This paper aims to clarify the main types of plastic materials available and the application of each material.
1.Different types of plastic materials
Plastic is a widely used synthetic material, typically made from petrochemicals but can also be made from some natural ingredients. Common plastics include nylon, acetal, and high-density polyethylene. Plastics can be divided into two main types: thermoplastics and thermosetting plastics, but we will focus on grouping them based on their mechanical properties for discussion.

a. Rigid plastics
In short, these are the plastics we use for projects such as electronic casings, football helmets, and power tool bodies. They are not as elastic as rubber, but much stronger. They are typically graded according to the Shore D scale. Some common types of rigid plastic are ABS, nylon, HDPE, and polycarbonate.
b. Elastomer
They are “elastic”. Some common elastomers include silicone rubber, HNBR, nitrile rubber, and polyurethane rubber. The part shown in the picture below is made of a liquid silicone rubber compound.
c. Fiber reinforced plastics
These plastics have dispersed reinforcing fibers to increase hardness, strength, and wear resistance. Common examples include glass fiber and carbon fiber layers. The use of short chopped fibers in injection molded plastics is also common. The picture below shows a pocket knife with a handle made of nylon plastic and glass fiber fillers. The knife has been carried daily for over two years with almost no wear, thanks in large part to the mechanical properties of the glass-filled plastic. Some SLS printed parts may have glass-filled nylon powder, which results in much higher hardness than standard nylon.
d. Modified plastics with additives
It is also common to add additives to base plastics to produce various desired characteristics. Some common additives include antimicrobials, antistatics, plasticizers, pigments, UV stabilizers, fillers, and flame retardants.
2.Mechanical performance of plastic
Regardless of the type of plastic, it is necessary to have a basic understanding of material properties to choose the best material.
This is the maximum stress that can be applied before permanent deformation of the material occurs. In almost all cases, the stress applied to the material during its use should be kept below the yield strength of the material. If the stress is too high, the part will experience permanent deformation.
Also known as the modulus of elasticity, this is the amount by which a material will “stretch” when force is applied. If we keep the force below the yield strength, the part will return to its original shape once the force is removed. Elastic materials are also commonly used for washers and seals, such as those in blender and travel coffee cup lids.
c. Hardness
Different plastics and rubbers have different hardness values, typically measured using the Shore hardness scale. In the Shore hardness scale, hardness is divided into three categories in order of increasing hardness: 00, A, and D. An eraser has a hardness of around 40 on the Shore A scale, while a plastic safety helmet has a hardness close to 80 on the Shore D scale.

d. Friction coefficient
Friction coefficient is a term that describes the sliding behavior of a material. This is particularly important for projects that involve sliding or dynamic contact. Some bearings, for example, are made of polytetrafluoroethylene (PTFE) material due to its low friction coefficient.
3.Determining the purpose of plastic parts.
a. Different plastics are suitable for different purposes
Some applications are mechanical, wear-resistant, or elastic. Different materials should be selected according to different applications. It is wise to choose relatively cheaper materials with similar performance. Some plastic materials have long-term reserves at the supplier, but others require special orders.

b. Consider the availability of materials
Materials such as sheets, rods, or tubes (for example, used for CNC machining) or printable materials used for FDM are available. Typically, FDM machines try to match the best choice of the final production material. You can simulate some plastics using other 3D printing options (such as SLA or SLS), but materials that match the final production completely are usually not available. SLA materials start as a liquid and are cured by laser exposure, which can result in some inherent differences in the final product. Similar to SLA, the difference with SLS is that powder is used to fuse the material with another surrounding powder through laser impact. SLS may be a good option if the final production material is nylon.

c. Considering the processing capacity of plastics
Similarly, some plastics are better suited for CNC machining (such as polypropylene), while others can be easily 3D printed, with different processing methods. The price of plastic prototypes may vary.
d. Consider plastic recyclability
If so, make sure to use thermoplastic instead of thermosetting materials.
4.Plastic materials commonly used in prototype manufacturing
I. PMMA
You may have never heard of a polymer name as complex-sounding as PMMA, but you have heard of acrylic glass. It’s easy to understand, as it’s ubiquitous in car headlights, windows, displays, lamps, and more.
i. advantage
The transparency and corrosion resistance of PMMA make it widely used in our daily lives. In addition, this material is highly processable and can be cut, cast, or molded by CNC. It is strong, dimensionally stable, and can operate at temperatures up to 160 degrees Celsius.

ii. defect
Despite being tougher than glass, PMMA is still relatively brittle compared to other plastics. It also swells when in contact with water, and can be dissolved by hydrocarbons.
iii. Range of use
PMMA is widely used as a substitute for glass, which is prone to breakage. Examples include traffic lights and car lights. Acrylic glass is also commonly used for experiments and demonstrations. It has broad applications in medicine, and many medical devices are made of PMMA because of its transparency and durability. Some lenses are even made of PMMA. If you are looking for excellent transparent parts or prototypes that can be polished to look just like glass, or if you want to project light into a transparent enclosure, you should definitely consider PMMA.

II. Nylon
Nylon has flexibility and strength, and its excellent properties make it suitable for producing fibers. Yes, you are sometimes wearing plastic clothes.
i. advantage
Nylon is highly flexible and at the same time very strong, with excellent abrasion resistance and no tendency to shatter. It is also very lightweight and has a high temperature resistance, even higher than PMMA, with a maximum of up to 195 degrees Celsius.
ii. defect
Nylon is not as strong in resisting chemicals and corrosion. Some acids, alkalis, and other strong liquids can dissolve it. It is also less effective in sunlight, with ultraviolet radiation weakening its microstructure. Like PMMA, it swells in water. It also has a high shrinkage rate.


iii. Range of use
The most important application is in car tires. Due to its high strength and good wear resistance, nylon is often used in parts that experience friction. If you need parts for bearings or gear mechanisms, nylon is a good choice.
III. ABS
With the rise of additive manufacturing, ABS has become very popular recently due to its low shrinkage rate, good molding performance, and relative affordability. Currently, ABS is one of the main plastics used for rapid prototyping.
i. advantage
ABS has resistance to most acids and alkalis, which is weaker in other plastics. It is very glossy, so if you want your product to be glossy, you should consider ABS. In addition, ABS also has shock resistance.
ii. defect
ABS is not as strong as other plastic materials. Secondly, the working temperature of ABS is very low, less than 90 degrees Celsius. It is slightly toxic, so using it for toys or children’s products is not a good idea.


iii. Range of use
It’s cheap and molds well, making it ideal for 3D printing or injection molding, so many custom or 3D printed parts are made from it. Due to its glossy finish, some electronics and phones use it to make the casing. If you don’t have the most generous budget, or you’re really unsure about the design, I suggest using ABS for 3D printing or CNC machining your prototype, so you don’t have to pay a lot of money.
IV. POM
Compared to other plastics, POM possesses properties that are most similar to metals, which makes it highly suitable for large volume parts as it maintains its lightweight characteristics.
i. advantage
POM has high strength and fatigue resistance, as well as excellent high-temperature stability (up to 166 degrees Celsius). It is extremely hard, corrosion-resistant, and has good friction properties. It is also one of the few plastics with high moisture resistance.
ii. defect
The most intimidating aspect is its uneven shrinkage, which can be difficult to predict and cause trouble when it is cast or molded. In addition, this plastic is very hard, which can dull CNC cutting tools when cutting the material.


iii. Range of use
POM has very high tensile properties and is therefore often used in engineering parts and machinery. For example, plastic pumps, because it has a great friction performance. Some components that frequently absorb moisture are made of POM, so they won’t expand.
V. PC
PC has been competing with glass and PMMA. If you are making transparent parts or prototypes, PC is one of the appropriate plastic materials. It can also be colored to make colored glass, and even make some opaque decoration.
i. advantage
The seismic resistance of PC is much higher than that of PMMA or glass. This material has high heat resistance and can work at temperatures above 150 ℃.
ii. defect
PC will perform poorly under ultraviolet light, and may lose transparency under long-term exposure. It is also easy to be scratched, and the clear prototype will be covered with special film. PC should not be used for food or organic matter, because it will emit some harmful vapors over time.
iii. Range of use
Any transparent parts can be made of PC and PMMA, such as car lamps or reinforced glass. It is a widely used material for rapid prototyping, much more than PMMA. It is relatively cheaper to make PC prototypes. If you want a really high-strength transparent or colored plastic prototype, you should focus on PC.
5.Find the suitable plastic prototype manufacturer
When you are not sure which material to use to make your plastic prototype, please remember to find a professional manufacturer to help you solve all problems. Perhaps you are confused, how to find a professional prototype manufacturer? Now is the era of information superhighway. Maybe we can find the answer by using “Google”, the world’s largest search engine. Some professional prototype manufacturers will have their own official websites. Determine whether they are suitable partners by browsing their website expertise.


DDPROTOTYPE is committed to becoming a professional plastic prototype manufacturer and providing CNC plastic machining services with high cost performance for customers around the world. Learn more about our plastic prototyping. You can easily upload your CAD file today to get a free quotation.