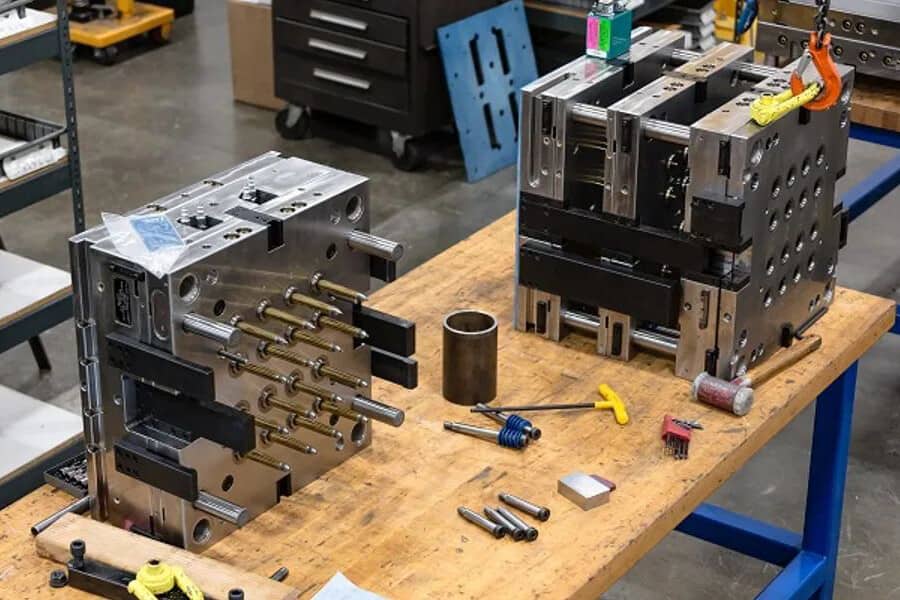
Rapid Prototyping & Rapid Manufacturing Expert
Specialize in CNC machining, 3D printing, urethane casting, rapid tooling, injection molding, metal casting, sheet metal and extrusion
Let’s Learn About Aluminum Injection Molding
The potential of aluminum injection molding has been fully exploited. Compared with steel injection molding it has more advantages under the right circumstances. Also it has become a hot topic in the field of injection molding. Traditional injection molding typically uses steel molds capable of producing millions of parts, however, making a mold typically takes months also with a great expense. Some require an investment of $50,000 or more. What if the quantity produced is thousands of parts? The average price competitiveness per part will be greatly reduced. Then aluminum injection molding would be the ideal choice, offering better quality, less scrap, faster cycle times, tight tolerances and consistency, reducing production costs. In this article, we will detail some advantages and disadvantages of aluminum molds and steel molds.
1. Small batch production by using aluminum molds
Manufacturing aluminum molds within 15 days or less.
Low manufacturing cost, about $1,
Production quantities up to 10,000 or more; provide higher value for small batch production.
1 cavity, 2 cavity, 4 cavity and 8 cavity can be designed.
Compatible with more than 100 different materials, including ABS, PC, PP, LCP, POM and liquid silicone rubber.
Excellent heat dissipation, avoid messy cooling lines.
The heating and cooling speed of the aluminum mold is seven times as much as steel mould, to produce more parts per unit time.
There is no maintenance fee for mold damage, and it will be replaced for life

2. Use steel molds for mass production
When the production parts are hundreds of thousands to millions, the unit cost ofpart can be reduced.
Durable, can produce millions of parts at one time.
Suitable for multi-cavity moldswith more than 8 cavities.
Complex geometry parts can be produced.
More surface treatment options such as texture and pattern.
More material options, such as glass, fiber and other materials mixed with other additives

3. Summarize.
How to choose between aluminum molds and steel molds is depends on your project. Steel molds are a more common option, but if your supplier has more experience with aluminum molds, doesn’t require millions of parts, requires a shorter timeframe to get the product to market, and wants to avoid venture capital until the part design is truly proven, just feel free to use aluminum injection molding for small volume production, it’s a good choice.


